The process limits in sheet metal forming are not only determined by the material, but also by the prevailing friction and lubrication conditions. Due to the increasing complexity of industrial sheet metal components and the increased use of higher strength materials, tribological boundary conditions are of great importance. Due to the complexity of the interactions, it is only possible to use friction as an integral state variable to describe the tribological conditions if the underlying tribosystem is taken into account.
For economic and metrological reasons, it is usually not possible to measure friction in industrial sheet metal forming processes. This can be overcome by simulation tests such as the strip drawing test. Here, relevant properties of industrial sheet metal forming tribosystems are physically simulated and the friction is determined in the form of friction values. The following figure shows a photo and the basic principle of the strip drawing test at the PtU.
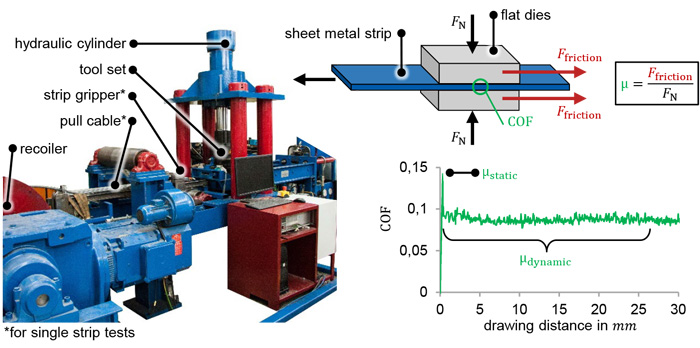
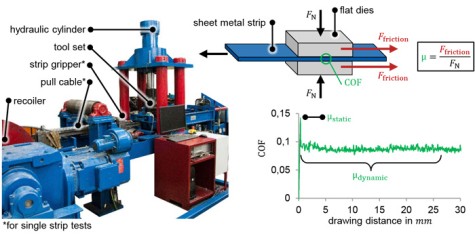
The dies of the strip drawing test can be heated or actively cooled. Automatic lubrication systems are available for tool and sheet lubrication. The strip drawing test at the PtU complies with the VDA specification 230-213 and has been further developed for aluminum hot forming in the years 2018 to 2023. In addition to varying the contact normal stress, the drawing speed and the amount of lubrication, the sheet metal strips can be heated to temperatures of up to 550 °C. The following figure shows the schematic sequence of a strip drawing test with sheet lubrication or alternatively with sheet heating and die lubrication. The tests can be performed with single strips or, in the case of large test series, in coil operation. Numbers I through IV indicate the test sequence.
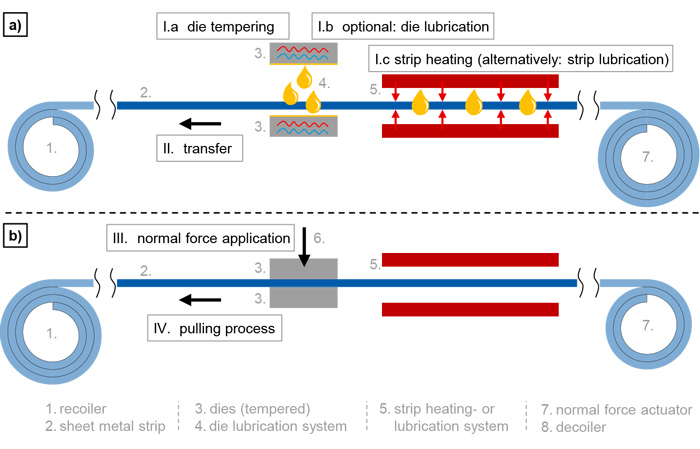

Technical data
- Normal force: 1 kN to 380 kN
- Pulling force: max. 60 kN
- Pulling speed: 1 mm/s to 450 mm/s
- Die temperature: 15 °C to 450 °C
- Sheet temperature: max. 550 °C
- Die dimensions: 40 mm x 40 mm to 150 mm x 80 mm