The sliding compression test is a tribometric test stand for direct determination of friction forces.
Description of the test principle
Due to the high contact normal pressure as well as the high surface expansion rates which can be reached due to specifically designed die cavities, this test stand is very well suited to determine friction coefficients for massive forming operations. The application of the normal stresses and the measurement of the friction forces are conducted separately in the sliding compression test. After insertion of the test specimen, the specimen is compressed. Subsequently, after completing the compression, the plate is, as described schematically in the following figure, slid in relative motion against the specimen whilst the compression force is maintained. However, it is also possible to vary the compression force during the sliding cycle. Likewise, the sliding velocity can remain constant or be varied.
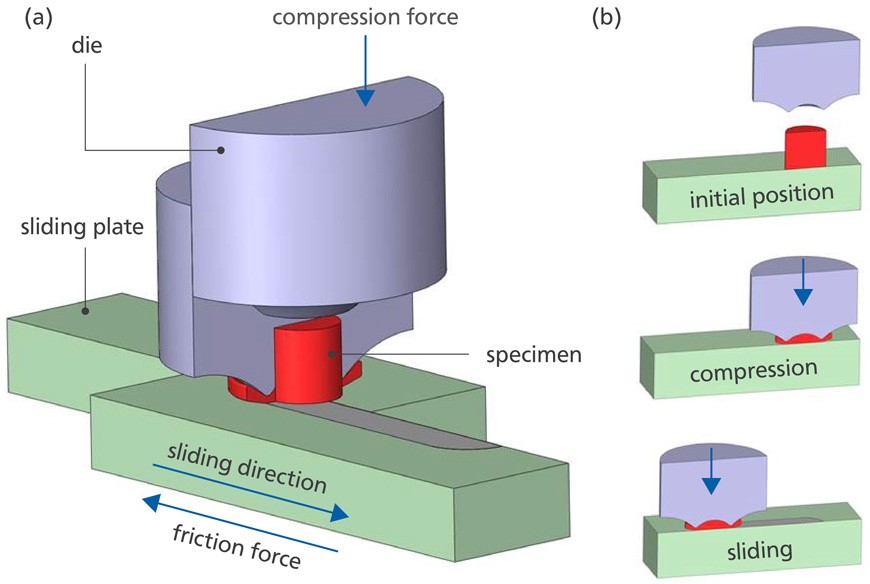
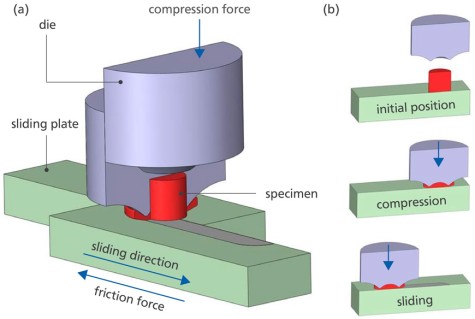
With the described sequence, it is thus possible to determine friction forces in dependence of different loading cases. By direct measurement of the friction forces during the sliding cycle, it is possible to determine the friction force in dependence of the sliding distance. Different tribological systems as well as tool and work piece materials can be investigated, therefore enabling a good reproduction of the occurring industrial conditions in cold forming operations.
The sliding compression test stand at the PtU
The sliding compression test stand (depiction see figure below) consists of a dual acting hydraulic press with a maximal compression force of 1,000 kN. Friction forces of up to 665 kN during the gliding cycle can be applied. The sliding velocity can be set up to 500 mm/s while the sliding displacement can reach up to 100 mm. With this set-up, normal contact stresses can reach up to 3,000 N/mm2 for non- and low-alloyed steel. With available die cavities, surface expansion rates of up to 11 are reached.
Heating of work pieces and tools
To investigate the temperature dependence of tribological systems as well as to reproduce the industrial process conditions, possibilities to heat up the sliding plates as well as the specimens are available. Heating cartridges are used to heat up the sliding plates to a maximum of 400°C. The heating of the specimens is carried out with the help of an induction heating system (as depicted) or with a conventional furnace for temperatures of up to 1200°C. Measurement of the temperature is carried out with the help of optical measuring systems: infrared camera ThermaCAM S65 (FLIR Systems) or Pyrometer Optris CTLaser LT with CF2-Optics 75:1, see figure below.
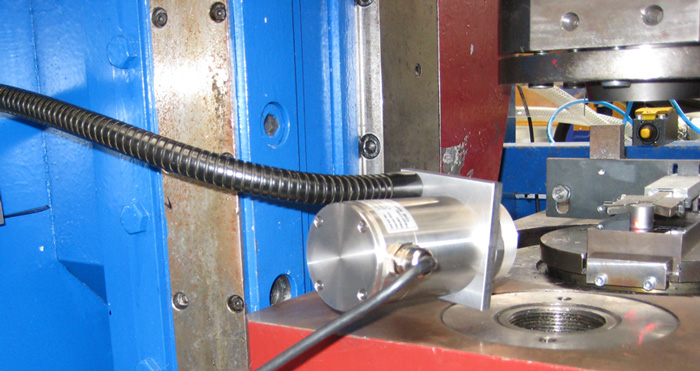
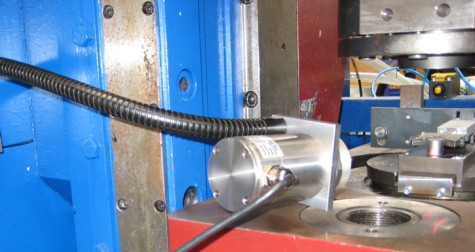
References
The sliding compression test stand has been used to determine the influence of macroscopic lubricant pockets on the surface of sliding compression specimens. It was shown that it is possible to decrease the friction forces through this optimization of the work piece surface. Furthermore, a friction model was developed which allows to determine the surface evolution of the work pieces numerically. In additional studies, the influence of the sliding velocity as well as the temperature within the contact zone was determined.