Based on the researches of linear flow splitting and linear bend splitting a new forming process has been developed to enhance the process limits of the existing linear, continuous process. The flexible flow splitting enables the production of bifurcated sheet metal parts in integral style with varying cross-sections in lengthwise direction and non-linear progression of the bifurcation line.
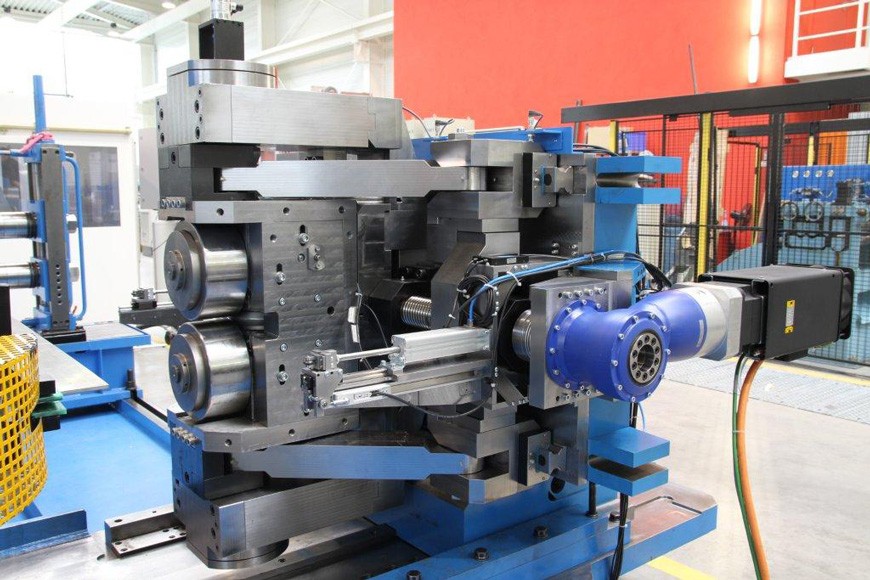
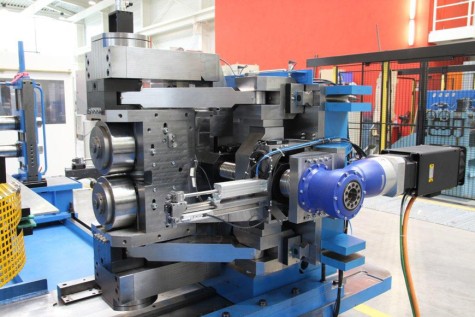
A special forming stand has been developed and constructed providing additional degrees of freedom to the tooling system. To follow a non-linear contour of the band edge during the forming process these additional degrees of freedom are essential. Rotation and translation of the tooling system unit are provided by a parallel geometry, providing precise positioning despite high process loads on the splitting roll.
In multiple steps, parts with integral bifurcations along a non-linear curvature can be manufactured controlled by open loop or closed loop process guidance. The progression of the band edge can be composed of linear sections that are parallel or inclined to the feed direction as well as of convex and concave radii and tangential transitions.
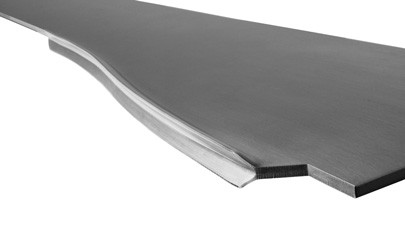
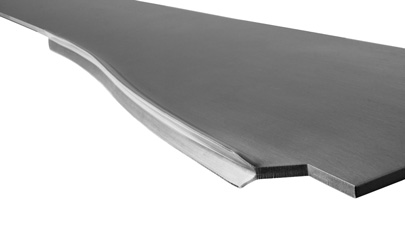
Due to varying cross-sections, this process is subject to transient conditions regarding process forces and tool work piece interference. Variable loads on the splitting roll and the captured band edge contour as well as the derived tool paths are recorded. The cross-section geometry along feed direction is measured by an optical measurement system.
Technical data
- Sheet thickness: 2 mm < 6 mm
- Sheet width: 490 mm – 600 mm
- Sheet length: < 1600 mm (blank operation)
- Inclination angle: max 15° (only for medium sheet widths)
- Sheet edge radius: 350 mm – 2485 mm
- Continuous edge necessary