ConTRoll – Controller for Profile Straightening in Flexible T-Profile Rolling
The project focuses on the development of a model-predictive control strategy to be able to compensate for side effects in flexible forming processes inline and to produce dimensionally stable components. The control system should be able to deal with the increased complexity of the overall system and with dead times due to the difficulty of measuring the component properties in the forming process. This will be demonstrated using the example of flexible T-profile rolling to straighten unwanted profile curvatures. The aim is to make the new process suitable for industrial use, increase the degree of automation and thus produce aircraft stringers in a more environmentally friendly and resource-saving way in future.
Motivation
In accordance with the lightweight construction concept, flexible processes enable more efficient utilisation of materials through the production of load-oriented components. The implementation of flexible forming processes and the associated machines is based on the addition of driven degrees of freedom for the relative movement of the tool and workpiece. The additional degrees of freedom require customised controls and regulation. However, this results in undesirable, variable side effects such as profile errors. The cause of the profile errors lies in unintentionally introduced stress differences in the component, caused by the change in geometry. This project aims to compensate for these side-effects, whereby flexibility is considered from the mould path to the finished product. The particular challenge is that in forming technology, process errors only occur downstream, forces and moments as well as framework compliance are increased and it is difficult to measure the component properties in the process.
The control system is to be developed using the example of flexible T-profile rolling, a new process for rolling stringers in aeroplanes. In flexible T-profile rolling, variable material thicknesses are applied to a T-profile over its length. The varying profile bowings that result from the flexible thickness transitions are to be measured and corrected inline so that straight T-profiles are produced. The aim of the project is to develop a control system based on an analytical model to be developed for predicting the straightening parameters and a measurement system for measuring the bowing.
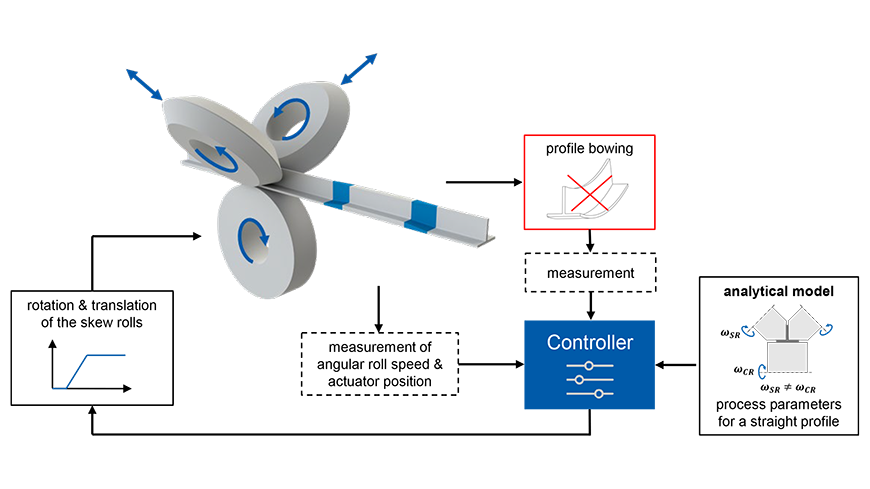
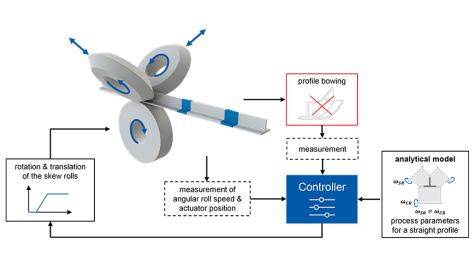
Approach
The project focuses on the development of a model predictive control system to compensate for side effects in flexible forming processes inline and to produce dimensionally accurate components. This is to be tested using the example of flexible T-profile rolling in order to make the new process suitable for industrial use and increase the degree of automation at the same time. In flexible T-profile rolling, the varying radii of the skew rolls result in an inhomogeneous longitudinal strain distribution across the profile cross-section, which causes the profile bowing. The bowing can be straightened by varying the angular speeds of the skew and cylindrical rolls. An analytical model is to be developed in order to be able to predict the required straightening parameters as a function of the resulting bowing. This will be achieved through the use of numerical simulations, which will be carried out and experimentally validated for this purpose.
In addition, the system is to be equipped with sensors to record the straightness deviations of the profiles, the roll positions and roll angular speeds and transmitting them back into the drive movement in real time. The target speed required for straightening is to be calculated from the measured bowing and the specified thickness profile using the analytical model to be developed by the PtU. This should then be controlled by comparing it with the actual measured angular roll speed. This is illustrated in Figure [1] for clarity. The control is implemented by the project partner TriLogiX.
Acknowledgement
The ConTRoll project is funded by the German Federal Ministry of Economics and Climate Protection (BMWK) as part of the Central Innovation Program for Medium-Sized Businesses (ZIM). Additional thanks go to the project partner TriLogiX.
Funded by
Project Partners