Sensorless wear detection – Forming tool with sensorless detection of wear
The increasing use of high-strength and ultra-high-strength steels leads to increased stress on sheet metal forming tools. As a result, tool wear increases and tool life decreases. By using thermoelectric measurements, the wear progress can be recorded inline directly in the contact zone without the use of an additional sensor. The aim of this research project is to ensure that tools with the ability to detect wear inline using thermoelectric measurement are robustly dimensioned.
Motivation
The efficiency and competitiveness of small and medium-sized enterprises (SMEs) in the sheet metal working industry depends to a large extent on effective control of tool wear. However, modern lightweight materials and high-strength steels, which are increasingly being used in forming, pose a challenge. Adapting the required process forces to the material strength leads to increased tool wear and shorter tool life, which impairs production processes. From an ecological point of view, it is also important to optimise modern production technology in terms of its environmental compatibility and resource efficiency. However, many performance-enhancing components of lubricants are difficult to reconcile with this requirement. Conversely, the reduction of these environmentally harmful components leads to a loss of performance and premature wear. For SMEs working at the limits of formability, early detection of tool wear is crucial to avoid costly breakdowns and production errors, and to minimise the risk of early and sudden tool failure and further pave the way towards resource efficiency, real-time monitoring of wear development is required. This project aims to adapt a method for sensorless wear detection using thermoelectric measurements to the conditions in real forming processes. This method enables real-time monitoring, optimises maintenance intervals and reduces costs as expensive sensors can be avoided. This opens up opportunities for SMEs to deal effectively with tool wear and ensure more sustainable production.
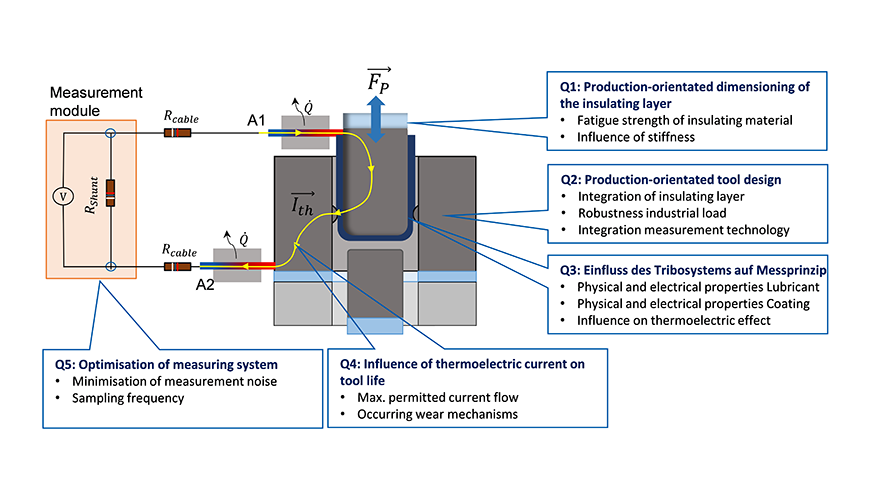
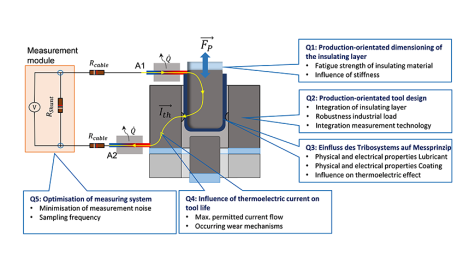
Approach
At the beginning of the project, the existing industrial boundary conditions will be concretized using an ironing process as an example process. Ironing processes are subject to high tribological loads and are therefore highly susceptible to wear. The first step is to identify insulating materials that meet the requirements of the real forming process. The requirements for the insulating materials result from the tool load, the required component quality, the service life and the inline measurement concept using the thermoelectric current. The influences of the wear-protective coatings and lubricants used in the industrial example process are then investigated. The aim is to identify advantageous properties of lubricants and tool coatings for reliable wear detection using thermoelectric measurements. Based on this, a forming tool with a measuring system will be designed and manufactured for an example process. The maximum permissible current flow is determined to determine the appropriate measuring frequency. The designed tool is then tested both in the laboratory and in a real production environment. Depending on the knowledge gained, further investigations into the insulation materials may be necessary. The main research questions and the schematic representation of the tool are shown in Figure [1].
Acknowledgement
The research work presented here is part of the IGF project no. 01IF23045N of the research association Europäische Forschungsgesellschaft für Blechverarbeitung e.V. (EFB). This is funded by the German Federal Ministry of Economics and Climate Protection (BMWk) via DLR as part of the programme for the promotion of joint industrial research (IGF) on the basis of a decision by the German Bundestag.
We would also like to thank all industrial partners who support the research project in the project support committee.
Funded by
Network
Project Partners