Sensorlose Verschleißdetektion – Umformwerkzeug mit sensorloser Detektion von Verschleiß
Zunehmende Verwendung von hochfesten und höchstfesten Stählen führt zur erhöhten Beanspruchung von Werkzeugen der Blechumformung. In der Folge steigt der Werkzeugverschleiß wodurch die Standzeiten sinken. Durch den Einsatz thermoelektrischer Messungen kann der Verschleißfortschritt direkt in der Kontaktzone ohne die Verwendung eines zusätzlichen Sensors inline erfasst werden. Das Ziel dieses Forschungsvorhabens ist es, dass Werkzeuge mit der Fähigkeit zur Inline-Verschleißdetektion durch thermoelektrische Messung robust dimensioniert werden.
Motivation
Die Effizienz und Wettbewerbsfähigkeit kleiner und mittlerer Unternehmen (KMU) in der Blechverarbeitung hängt maßgeblich von einer effektiven Kontrolle des Werkzeugverschleißes ab. Moderne Leichtbaumaterialien und hochfeste Stähle, die vermehrt in der Umformung genutzt werden, stellen jedoch eine Herausforderung dar. Die Anpassung der erforderlichen Prozesskräfte an die Materialfestigkeit führt zu erhöhtem Werkzeugverschleiß und kürzeren Standzeiten, was Produktionsprozesse beeinträchtigt. Aus ökologischer Sicht ist es zudem unabdingbar, die moderne Produktionstechnik hinsichtlich ihrer Umweltverträglichkeit als auch Ressourceneffizienz zu optimieren. Allerdings sind viele leistungsmaximierende Bestandteile von Schmierstoffen mit dieser Forderung nur schwer vereinbar. Eine Reduktion dieser umweltschädlichen Komponenten senkt umgekehrt deren Leistungsfähigkeit und provoziert frühzeitigen Verschleiß. Für KMUs, die an den Grenzen der Umformbarkeit arbeiten, ist die frühzeitige Erkennung von Werkzeugverschleiß entscheidend, um kostspielige Ausfälle und Produktionsfehler zu vermeiden.Um das Risiko des frühzeitigen und plötzlichen Werkzeugausfalls zu minimieren und den Weg hin zur Ressourceneffizienz weiter zu ebnen, ist ein Monitoring der Verschleißentwicklung in Echtzeit erforderlich. Dieses Projekt zielt darauf ab, eine Methode zur sensorlosen Verschleißdetektion mittels thermoelektrischer Messungen auf die Gegebenheiten in realen Umformprozessen zu adaptieren. Diese Methode ermöglicht eine Echtzeitüberwachung, optimiert Wartungsintervalle und reduziert Kosten, da teure Sensoren vermieden werden können. Dies eröffnet KMUs Möglichkeiten, effektiv mit Werkzeugverschleiß umzugehen und eine nachhaltigere Produktion zu gewährleisten.
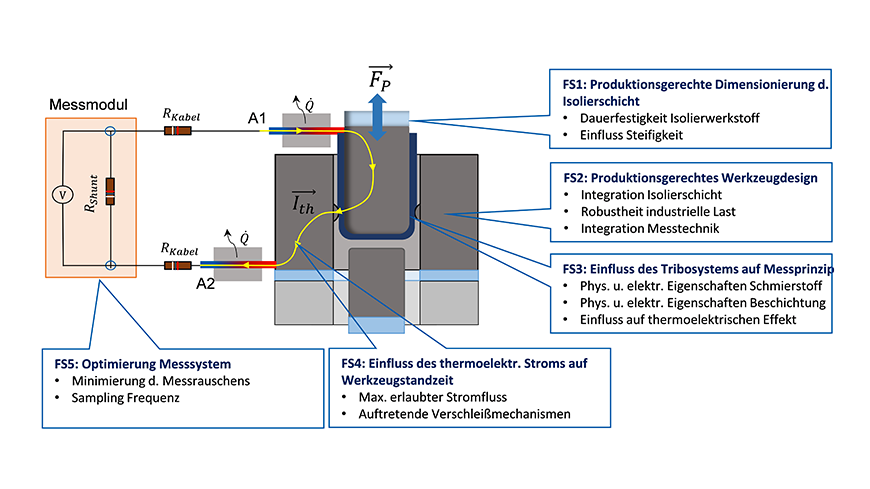
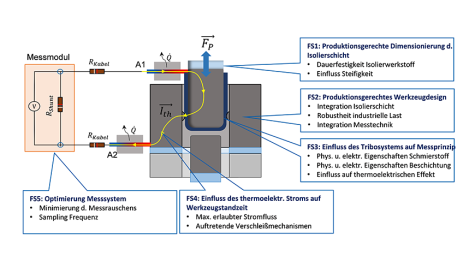
Lösungsweg
Zu Projektbeginn wird anhand eines Abtreckgleitziehprozesses als Beispielprozess die vorliegenden industriellen Randbedingungen konkretisiert. Abstreckprozesse weisen hohe tribologische Belastungen und infolgedessen eine hohe Verschleißanfälligkeit auf. Im ersten Schritt werden Isolierwerkstoffe identifiziert, die die Anforderungen des realen Umformprozesses erfüllen. Die Anforderungen an die Isolierwerkstoffe ergeben sich aus der Werkzeugbelastung, der geforderten Bauteilqualität, der Standzeit sowie dem Inline-Messkonzept durch den thermoelektrischen Strom. Anschließend werden die Einflüsse der im industriellen Beispielprozess genutzten, verschleißschützenden Beschichtungen und Schmierstoffe untersucht. Dabei sollen vorteilhafte Eigenschaften von Schmierstoffen und Werkzeugbeschichtungen für eine zuverlässige Verschleißdetektion durch thermoelektrische Messungen erkannt werden. Darauf aufbauend wird ein Umformwerkzeug mit Messsystem für einen Beispielprozess konzipiert und gefertigt. Zur Bestimmung der geeigneten Messfrequenz wird der maximal erlaubte Stromfluss ermittelt. Im Anschluss erfolgen Erprobungen des ausgelegten Werkzeuges sowohl im Labor- als auch im realen Produktionsumfeld. In Abhängigkeit von den gewonnenen Erkenntnissen können weitere Untersuchungen zu den Isolationswerkstoffen erforderlich werden. Die wesentlichen Forschungsfragen sowie die schematische Darstellung des Werkzeugs zeigt Abbildung [1].
Danksagung
Die hier dargestellten Forschungsarbeiten finden im Rahmen des IGF-Vorhabens Nr. 01IF23045N der Forschungsvereinigung Europäische Forschungsgesellschaft für Blechverarbeitung e.V. (EFB) statt. Dieses wird über die DLR im Rahmen des Programms zur Förderung der industriellen Gemeinschaftsforschung (IGF) vom Bundesministerium für Wirtschaft und Klimaschutz (BMWk) aufgrund eines Beschlusses des Deutschen Bundestages gefördert.
Ferner bedanken wir uns bei allen Industriepartnern, die das Forschungsprojekt im Projektbegleitenden Ausschuss unterstützen.
Gefördert durch
Netzwerk
Projektpartner