Multi-Cool – Robustification of multi-stage forming processes by active cooling
Multi-stage cold forming of complex sheet metal components made from high-strength materials leads to temperature increases of over 100 °C, making it difficult to maintain tolerances. Conventional tool cooling systems are limited in terms of their efficiency or their ability to reach hot spots in the tool. Additive manufacturing of tools, on the other hand, enables more flexible cooling channels close to surfaces that are to be tempered. A comprehensive analysis of the initial thermal state of the tools is used to develop new cooling concepts. The implementation of active cooling improves process stability and reduces rejects.
Motivation
Deep drawing is a key process in sheet metal processing that makes it possible to produce complex three-dimensional components. If the geometric complexity of a component exceeds the possibilities of a single-stage deep drawing process, multi-stage forming steps are required. These include not only deep drawing in a progressive drawing process to increase the drawing ratios, but also the combination with other processes (see Figure 1). The processing of high-strength materials with high forming ratios leads to significant temperature increases in tools and workpieces. The forming forces and frictional forces that act during the process are largely converted into thermal energy. During production, component temperatures can rise to 90-100 °C, making it difficult to maintain tight tolerances. The heat development has a negative effect on the dimensional accuracy of the tools, as the coefficient of thermal expansion of steel can lead to measurable deformations when the temperature changes. Stable, stationary processes are necessary in order to meet the increasing quality requirements and avoid rejects. The challenge is to implement effective cooling that meets the specific quality requirements of the components. In order to design the cooling efficiently, in-depth analyses are necessary to understand the interactions of all relevant factors and to find a technically and economically feasible solution.
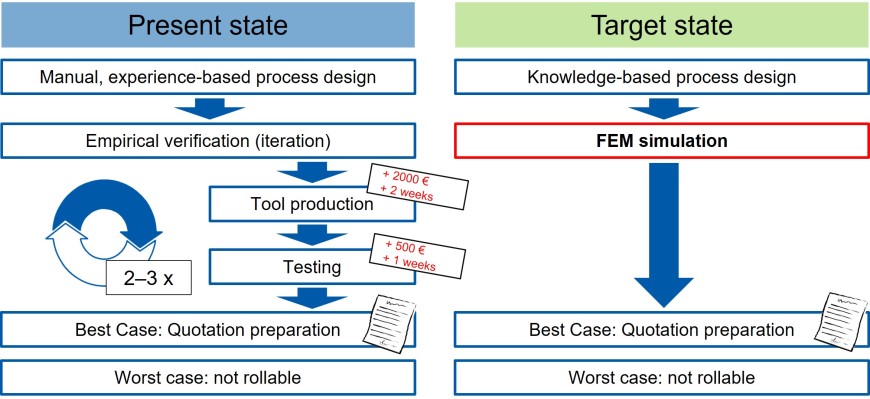
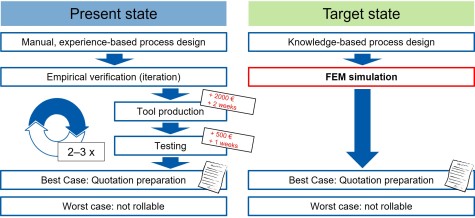
Approach
The project aims to develop design methods and manufacturing processes for cooled tools in multi-stage cold forming. Process stability and precise component specifications are to be improved through a deeper understanding of temperature development. First, a comprehensive analysis of the thermal state of uncooled tools and the current cooling configuration is carried out. A thermomechanical coupled simulation model will be created to determine relevant input parameters. Experiments with newly manufactured tool parts and sensors will validate the numerical results and investigate the temperature distribution throughout the manufacturing process. One focus is on the effects of thermal expansion on component tolerances, which are recorded by geometric measurements. In parallel, FKM is investigating suitable materials for rapid tooling, such as the materials 1.2709 and M789, with regard to their mechanical and technical properties, also taking into account compatibility with the rest of the tool in terms of corrosion and thermal expansion. Suitable heat treatments and coatings are evaluated in order to specifically influence these properties. At the PtU, it is also possible to harden tool surfaces in a targeted manner using machine hammer peening (MHP). The development of active cooling systems is intended to use resources efficiently and meet technical and economic requirements. Concepts for the integration of cooling channels in tool components are being developed, with additive manufacturing enabling innovative solutions. The possibility of targeted component cooling during transfer phases is also being investigated.
Acknowledgement
This research project is funded by the Hessen-Agentur under number 1482/23-35. We would also like to thank our industrial partners: Werner Schmid GmbH and FKM, who support the research project “Robustification of multi-stage forming processes by active cooling”.
Funded by
Project Partners