Residual Stresses – Application-specific adjustment of residual stresses during cold extrusion
The aim of this research project is to positively influence the residual stresses induced by forming by modifying the process control. The focus is on a full forward extrusion stage with a basic geometry based on an industrial component. The aim is to specifically influence the residual stress state of the component already in the forming process chain in order to optimise application-specific product properties such as mechanical distortion, static and dynamic strength, and resistance to stress corrosion cracking. To adjust the residual stress states, innovative tool systems with additional degrees of freedom are being further developed and adapted with suitable measurement technology. To transfer the forming strategies to the industrial environment, a further methodology, including validation for upgrading established tools, is being developed.
Motivation
In industry, residual stresses (RS) in production products are primarily perceived as a problem with potentially undesirable effects. The fact that targeted RS introduction can achieve performance increases without additional process steps is often not considered. Previous countermeasures have mainly been aimed at limiting the influences along the production chain. In particular, the negative effects of tensile RS on the surface, which are caused in the production chain, are to be avoided. Undesired RS are reduced, among other things, by stress relief using intermediate heat treatment. Approaches for the targeted adjustment of the RS state so far only exist in the form of additional operations such as deep rolling or shot peening and the associated increase in processing times and production costs. Although the results of the SPP2013 show that the performance of cold-formed components could be significantly improved by systematically optimizing the stress state during forming, the findings developed in the SPP have not yet been used industrially due to a lack of understanding and the lack of equipment. The biggest challenge for the industrial application of a system for setting tailored RS is the development of economically viable systems. In order to enable the transfer of the promising approaches and the transfer of knowledge to the industrial environment, it is therefore necessary to adapt the tool systems used for inline control of the ES state.
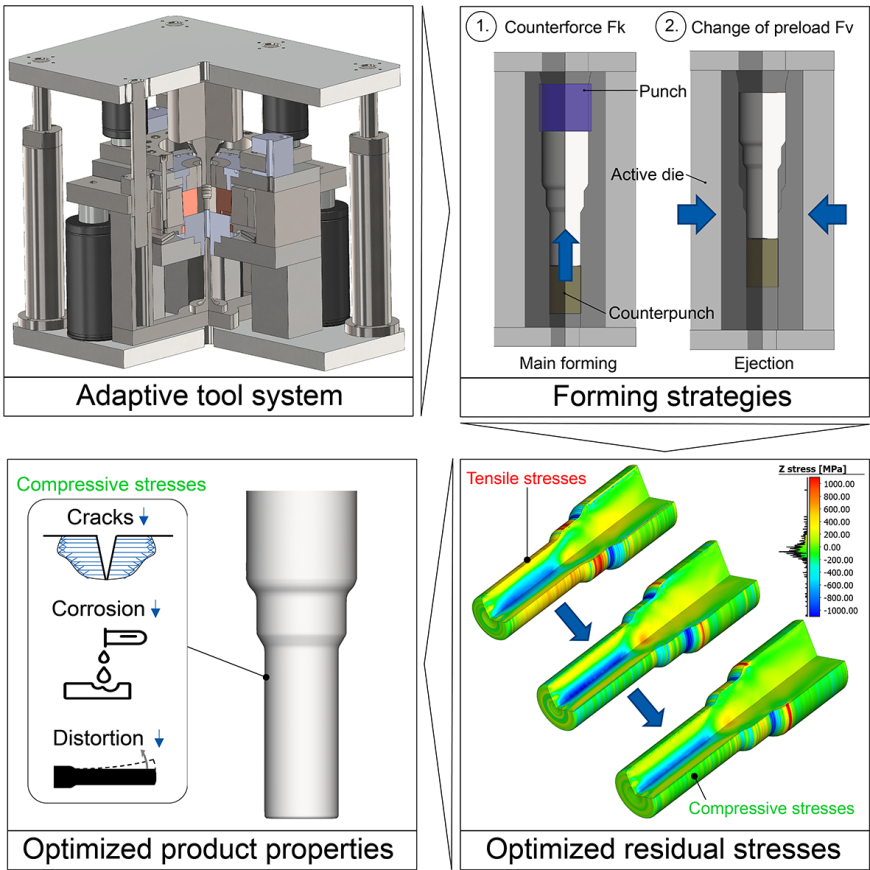

Approach
In order to resolve this conflict of objectives, an adaptive tool system is being developed in collaboration with the industrial partners Strecon A/S and Hirschvogel Umformtechnik GmbH. Based on defined requirements for the tool system, including fixed framework conditions from the reference process, suitable tool concepts are developed as part of an integrated product development process. The focus here is on concepts for process extension with an adjustable counterforce during the main forming operation and an adaptive change in the prestressing of the extrusion tool in the ejection phase. The targeted adjustment of these two variables will enable inline ES control. The combination of both forming strategies will be optimised using the finite element method and incorporating AI algorithms. Based on preliminary investigations on existing tool systems, a prototypical tool system will be developed and equipped with suitable measuring technology to implement the combined forming strategy. The improvements in properties achieved with the tool system will be confirmed by various validation tests, such as fatigue, corrosion and distortion tests, as well as hardness and residual stress measurements. The experimental investigations will then be used to derive a targeted control of the degrees of freedom for customised product properties. A comprehensive methodology is to be developed for transferring the forming strategies to industrial presses so that the concept can be used to retrofit conventional tools.
Acknowledgement
The presented transfer project is funded by the German Research Foundation (DFG) – GR 1818/86-1 – as part of the priority programme SPP2013 – ‘Targeted utilization of residual stresses in metallic components induced by forming’.
Furthermore, we would like to thank the companies Strecon A/S and Hirschvogel Umformtechnik GmbH for their active support of the project.
Funded by
Project Partner