CORNET-Wear-O – Wear optimization of highly stressed shaping tools
The use of higher and ultra-high strength materials for a more sustainable, resource saving as well as safer product design poses a great challenge to today's forming technology. To meet these requirements, the tool and die industry relies on carbide tools for bulk forming, which are used for example in the e-mobility industry or for lightweight construction of machine parts. The project aims to shorten the process chain for tool and mold making of carbide tools. In the process, the surface properties of the carbide tools are adapted to the expected loads during the manufacturing process.
Motivation
20% – 30% of the tools in solid forming are made of cemented carbide. In the conventional manufacturing process (Figure 1, above), standardized carbide blanks are first produced from powder, which must be machined by expensive and complex ablative processes such as hard machining or EDM to achieve the final geometry of the forming tool. Accordingly, the process chain involves two costly steps: The buildup and removal of carbide, which cancel each other out in the overall process. An additional coating provides increased wear resistance. Since the surface quality of the tool significantly determines the quality of the formed workpiece, forming tools are given a surface finish by means of polishing. Polishing of the tool surface is usually carried out manually by experienced employees of the tool manufacturer, which involves a considerable amount of time and limited reproducibility.
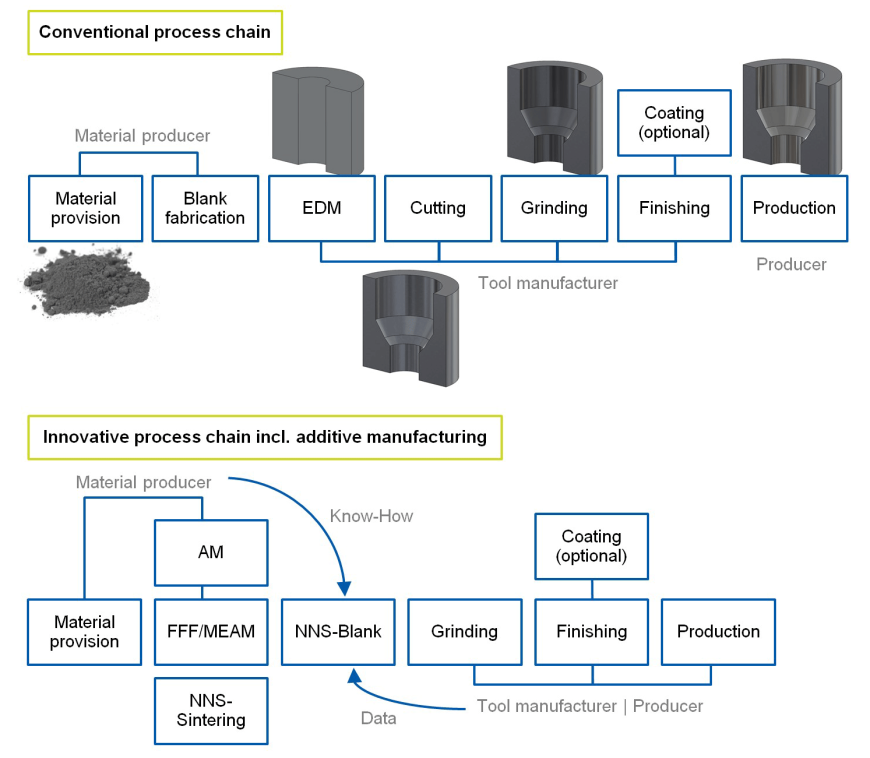
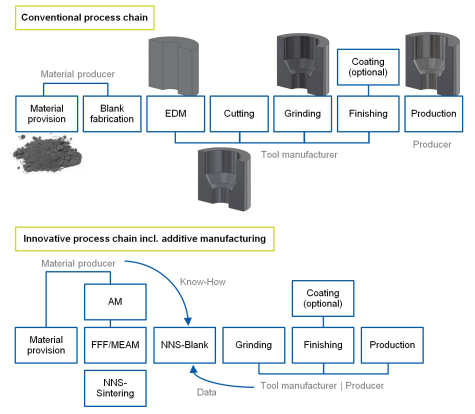
Approach
The aim of this project is to substitute the generation and ablation of carbide blanks by an additive manufacturing step (Figure 1, below). In this step, a near-net-shape blank (NNS blank) is directly generated from carbide powder. Additive processes such as 3D metal printing or processes with a negative mold of the NNS blank are available for this purpose. If a negative mold is used, the powder blank can additionally be compressed before sintering by means of machine surface hammering (MHP). Additive manufacturing processes thus provide a time and cost advantage over the conventional process. The use of machine surface hammering in finishing the mold surface offers further technological advantages. With the same surface properties, MHP requires only a fraction of the time of a manual polishing process. Furthermore, it can be used to produce specific tool areas to suit the stresses – by means of hardness enhancement through cold forming and the introduction of residual stresses.
Acknowledgement
The research work presented here is carried out as part of IGF project No. 268 EN of the Forschungsgesellschaft Stahlverformung e.V. (FSV). This is funded by the German Federal Ministry for Economic Affairs and Climate Action (BMWK) via the German Federation of Industrial Research Associations (AiF) as part of the program for the promotion of joint industrial research (IGF) on the basis of a resolution of the German Bundestag.
Furthermore, we would like to thank all industrial partners who support the research project “CORNET Wear-O” in the accompanying committee.
Funded by
Project Partners