CORNET-Wear-O – Verschleißoptimierung von hochbeanspruchten Umformwerkzeugen
Die Verwendung von höher- und höchstfesten Werkstoffen für ein nachhaltigeres, ressourcensparendes als auch sichereres Produktdesign stellen die heutige Umformtechnik vor eine große Herausforderung. Um diesen Anforderungen gerecht zu werden, setzt der Werkzeug- und Formenbau auf Hartmetallwerkzeuge für die Massivumformung, die zum Beispiel in der E-Mobilitätsbranche oder für den Leichtbau von Maschinenteilen eingesetzt werden. Das Projekt hat zum Ziel, die Prozesskette für den Werkzeug- und Formenbau von Hartmetallwerkzeugen zu verkürzen. Dabei werden die Hartmetallwerkzeuge durch ihre Oberflächeneigenschaften während des Herstellungsprozesses an die erwarteten Belastungen angepasst.
Motivation
20% – 30% der Werkzeuge in der Massivumformung werden aus Hartmetall gefertigt. Im konventionellen Fertigungsprozess (Abbildung 1, oben) werden zunächst standardisierte Hartmetallrohlinge aus Pulver erzeugt, welche durch teure und komplexe abtragende Verfahren wie Hartzerspanung oder Erodieren bearbeitet werden müssen, um die Endgeometrie des Umformwerkzeugs zu erreichen. Die Prozesskette umfasst demnach zwei kostenintensive Schritte: Der Aufbau und das Abtragen von Hartmetall, welche sich im Gesamtprozess gegenseitig aufheben. Eine zusätzliche Beschichtung sorgt für erhöhte Verschleißbeständigkeit. Da die Oberflächenqualität des Werkzeugs die Qualität des umgeformten Werkstücks maßgeblich bestimmt, erhalten Umformwerkzeuge ein Oberflächenfinish mittels Polieren. Das Polieren der Werkzeugoberfläche erfolgt meist manuell durch erfahrene Mitarbeiter des Werkzeugherstellers, was einen erheblichen Zeitaufwand und eine beschränkte Reproduzierbarkeit bedeutet.
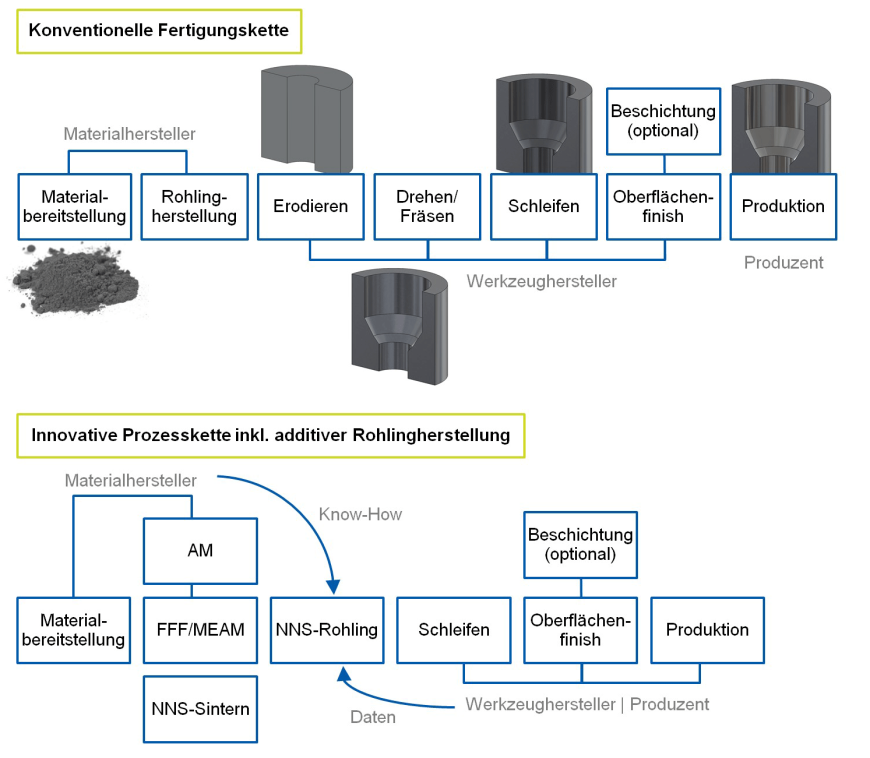
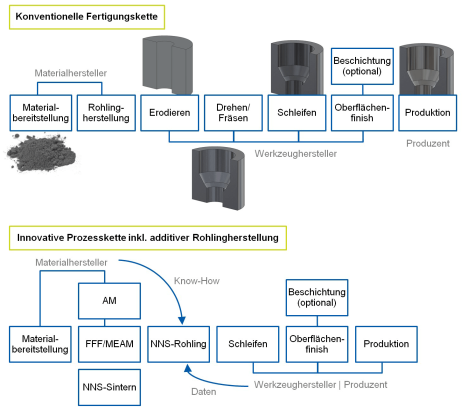
Lösungsweg
Das Ziel dieses Projekts ist die Substitution der Erzeugung und Abtragung von Hartmetallrohlingen durch einen additiven Fertigungsschritt (Abbildung 1, unten). In diesem wird aus Hartmetallpulver direkt ein endkonturnaher Rohling erzeugt. Dieser wird als Near-Netshape-Rohling (NNS-Rohling) bezeichnet. Dazu stehen additive Verfahren wie der 3D-Metall-Druck oder Verfahren mit Negativform des NNS-Rohlings zur Verfügung. Bei Verwendung einer Negativform kann der Pulverrohling vor dem Sintern zusätzlich mittels maschinellem Oberflächenhämmern (MOH) komprimiert werden. Durch additive Fertigungsverfahren entsteht somit ein Zeit- und Kostenvorteil gegenüber dem konventionellen Prozess. Der Einsatz des maschinellen Oberflächenhämmerns beim Finish der Werkzeugoberfläche bietet weitere technologische Vorteile. Bei gleichen Oberflächeneigenschaften benötigt MOH nur einen Bruchteil der Zeit eines manuellen Poliervorgangs. Weiterhin können damit gezielt Werkzeugbereiche beanspruchungsgerecht – mittels Härtesteigerung durch Kaltumformung sowie Einbringung von Eigenspannungen – gefertigt werden.
Danksagung
Die hier dargestellten Forschungsarbeiten finden im Rahmen des IGF-Vorhabens Nr. 268 EN der Forschungsgesellschaft Stahlverformung e.V. (FSV) statt. Dieses wird über die Arbeitsgemeinschaft industrieller Forschungsvereinigungen (AiF) im Rahmen des Programms zur Förderung der industriellen Gemeinschaftsforschung (IGF) vom Bundesministerium für Wirtschaft und Klimaschutz (BMWK) aufgrund eines Beschlusses des Deutschen Bundestages gefördert.
Ferner bedanken wir uns bei allen Industriepartnern, die das Forschungsprojekt „CORNET Wear-O“ im Projektbegleitenden Ausschuss unterstützen.
Gefördert durch
Projektpartner