RAmP – Tool-integrated local blank heating
For decades, high-strength aluminium alloys have been used as resource-efficient lightweight materials. Increasing the limited formability of these materials at room temperature by temperature-supported processes is already industrial practice. However, both hot and warm processes have a high time and energy cost. Therefore, in a series of LOEWE 3 projects, a new process route for tool-integrated blank heating is being developed. Within the framework of a dual doctorate together with Hörmann Automotive Gustavsburg GmbH (HAG) specific research questions are being addressed.
Motivation
Due to increasing legal requirements, the topic of lightweight construction continues to be of great interest in the mobility industry in order to reduce fuel and energy consumption as well as CO2 emissions. For commercial vehicles in particular, this allows a sustainable increase in payload. Fast-growing sectors such as the e-bike and automation industries also benefit from lightweight construction. In addition to efficiency improvements during operation, it focusses on utility benefits through higher dynamics (esp. automation) and handling advantages (esp. e-bikes).
High-strength aluminium alloy EN AW-7075 offers one possibility in the area of lightweight material design, however only allowing low degrees of deformation under cold forming conditions and thus simple components. For the production of more complex geometries, temperature-assisted processes are used, which are often cost-intensive and have limited reproducibility. The aim of the present project is to further develop the limited know-how for temperature-assisted forming of high-strength aluminium and to increase process robustness and productivity. Process design using high-performance numerical models is the basis for industrial application.
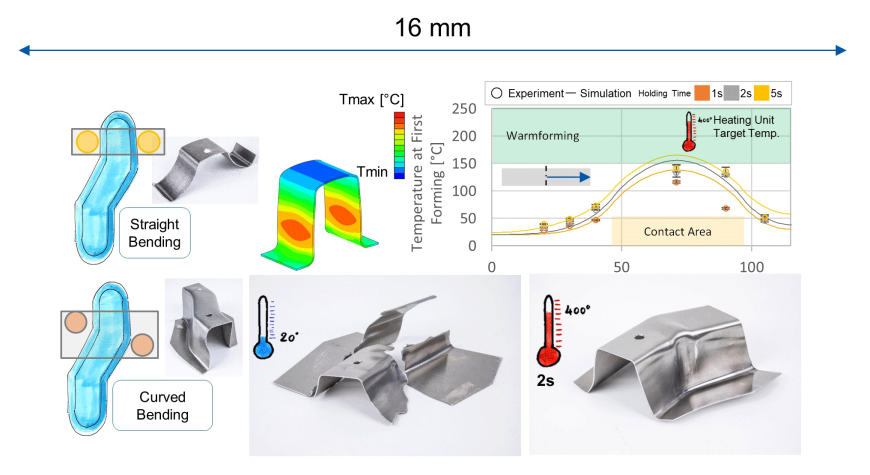
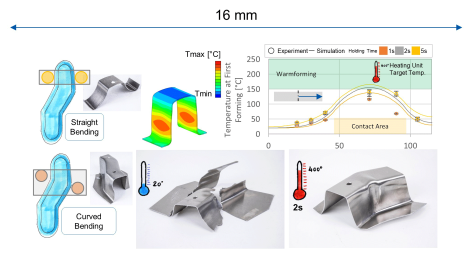
Approach
The aim of the project is the development and numerical simulation of a warm forming process with tool-integrated local contact heating of the blank. Due to the locally increased temperature, corresponding critical forming zones can be mitigated and more complex geometries can be realized with optimized resource consumption. The process route is implemented in a forming tool specially developed together with HAG. The flexible design allows the gradual increase of the component geometry towards an S-Rail benchmark geometry (straight bending, curved bending, deep drawing). Significant influencing variables are identified and robust multidimensional process windows are derived. The heat transfer between heated tool parts and sheet metal is particularly critical and will be investigated in a test rig developed at PtU. The knowledge gained will be used to build and validate a thermomechanically coupled simulation model. Target variables are temperature distribution, component geometry and end properties, see Figure 1. The project will conclude with the formulation of guidelines for the design of temperature-assisted forming processes and their application to potential components.
Acknowledgement
This project (combination of HA project no. 548/17-30 & 822/19-142 & 1269/21-170) is financed with funds of LOEWE – Landes-Offensive zur Entwicklung Wissenschaftlich-ökonomischer Exzellenz, Förderlinie 3: KMU-Verbundvorhaben (State Offensive for the Development of Scientific and Economic Excellence). We would also like to thank the companies involved in the project, in particular Hörmann Automotive Gustavsburg GmbH.
Funded by
Project Partner