Controlled joining – Position-controlled joining by forming on the example of optical sensors
In recent years, joining by forming has proven to be a particularly suitable technology for the damage-free integration of sensitive sensor elements into metallic load-bearing structures. Previous investigations based on rotary swaging have shown a high degree of mechanical design freedom for the manufactured sensor structures with suitable process design. However, these processes and product designs are limited to the integration of up to two-axis force/torque transducers. An extension of the measurement axis is achieved by optical non-contact measuring concepts. However, the substitution of electromechanical transducers by optical elements poses new process design challenges: In contrast to electromechanical transducers, which require specific stress conditions, the integration of optical transducers requires high positional accuracy. The research project aims to investigate a position-controlled forming joining process that in particular also enables the integration of optical six-axis force and torque sensors in load-bearing tubular structures.
Motivation
Load-bearing structures and machine elements with integrated sensors allow process forces and torques to be measured directly on the machine or tools without impairing their mechanical functionality. According to the state of the art, these structures are manufactured by integrating strain gauge-based or piezoelectric sensors into passive metallic structures, in particular by joining by plastic deformation. Due to the high design requirements for the sensors to be integrated and thus for the joining process, sensor structures manufactured by forming technology have so far been limited to one- or two- axis force or torque sensing. In addition, the manufacturing effort and energy consumption of the associated measurement chain increase almost linearly along with the number of measuring elements. In contrast, optical, non-contact measurement concepts enable multidimensional sensing of the occurring loads with comparably simple design requirements, low-cost components and with minimal space requirements. At PtU, an optical, image-based sensor concept was developed to extend the measurement axes of forming-based sensory load-bearing structures (see figure). Compared to strain gauge-based force and torque sensors, this concept is capable of measuring up to six degrees of freedom at significantly reduced overall measurement chain costs. However, the advantages of optical measurement concepts are accompanied by high tolerance requirements during assembly and thus demand a high degree of positional accuracy during structure integration.
Approach
An approach to achieving positionally accurate joining by forming is to ensure a force-fit and form-fit joining with lowest possible joining force through appropriate design of the joining partners. In this way, positional deviations due to high forming forces will be reduced. In order to achieve the required positional accuracy when joining, the second sensor part is position-controlled and integrated at the 3D-Servo-Press (3DSP) after optimal design of the joining partners. For this purpose, the position information or the current position deviations are acquired by the sensor to be integrated as image information and then quantified by means of an AI-based controller. The necessary position manipulation of the second sensor part can be carried out with the aid of the ram's degrees of freedom on the 3DSP. This way a position control joining can be achieved (see figure).
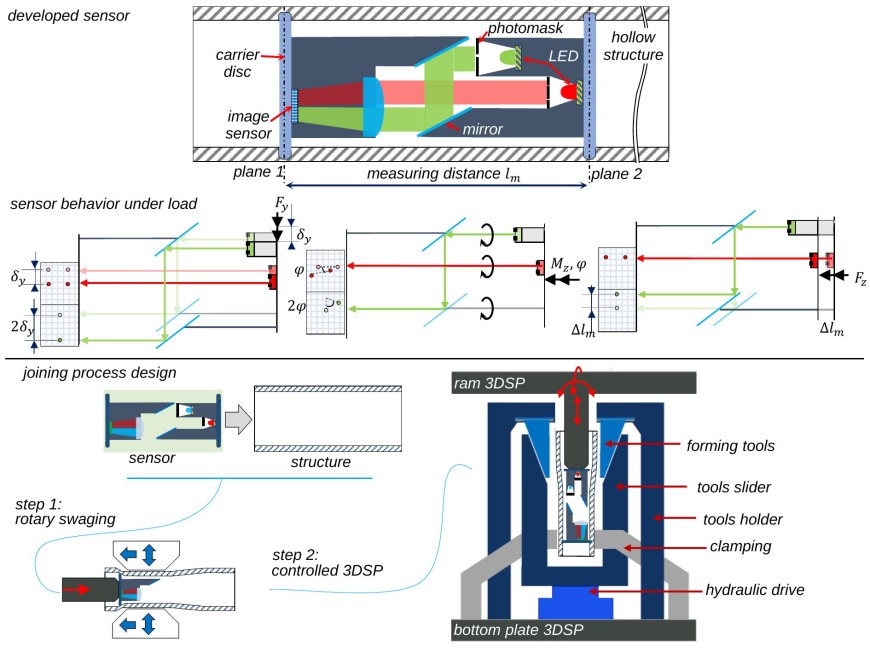
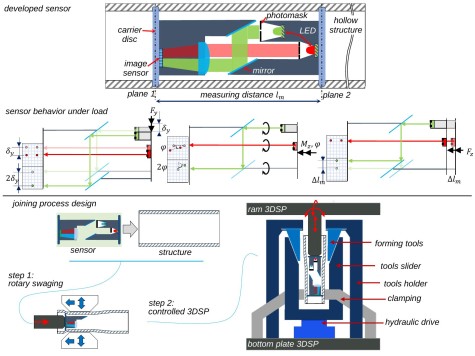
Acknowledgements
The presented research project is funded by the Deutsche Forschungsgemeinschaft (DFG, German Research Foundation) – Projektnummer (460244297).
Funded by