Innovative solution for production: Automated straightening of roll-formed profiles
2024/08/16
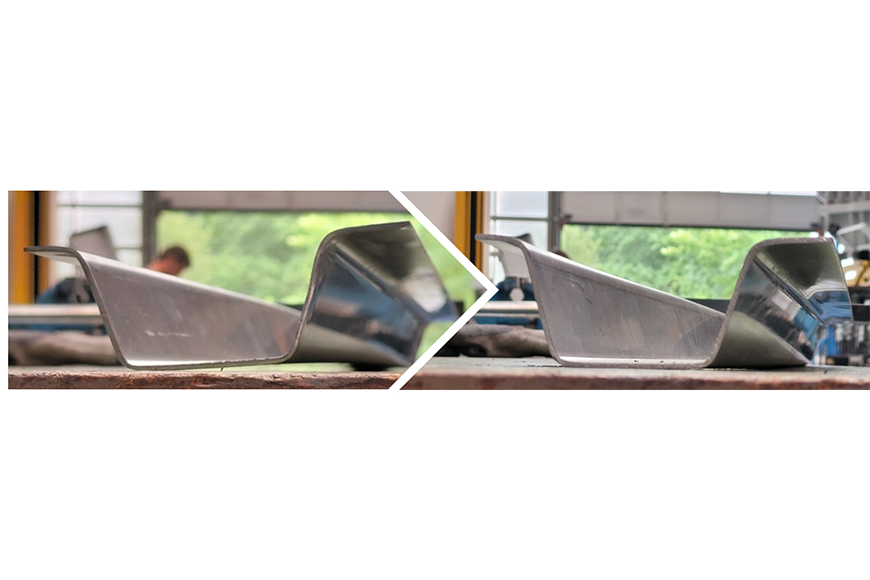
One of the biggest challenges in the production of roll-formed profiles are geometric tolerance deviations, which often lead to scrap. These deviations are caused by fluctuations in the material, faulty adjustment processes or unwanted introduced stresses during the process. Longitudinal defects such as bows and twists are particularly problematic and have so far been straightened manually and iteratively.
A newly launched aims to optimize this still very time-consuming process. By developing an analytical model, the direct correlation between longitudinal defects and the longitudinal strain distribution in the profile could be demonstrated. We want to use this knowledge to automate the straightening of profiles and make them inline-capable – using an innovative process called partial rolling. DFG transfer project
The aim is to straighten roll-formed profiles automatically and reliably by specifically influencing the longitudinal strain distribution through partial rolling. Supported by our project partner , we are developing new measuring technology for geometry recording and a special adjustable straightening device. This enables us to improve product quality and conserve resources. Tillmann Profil GmbH
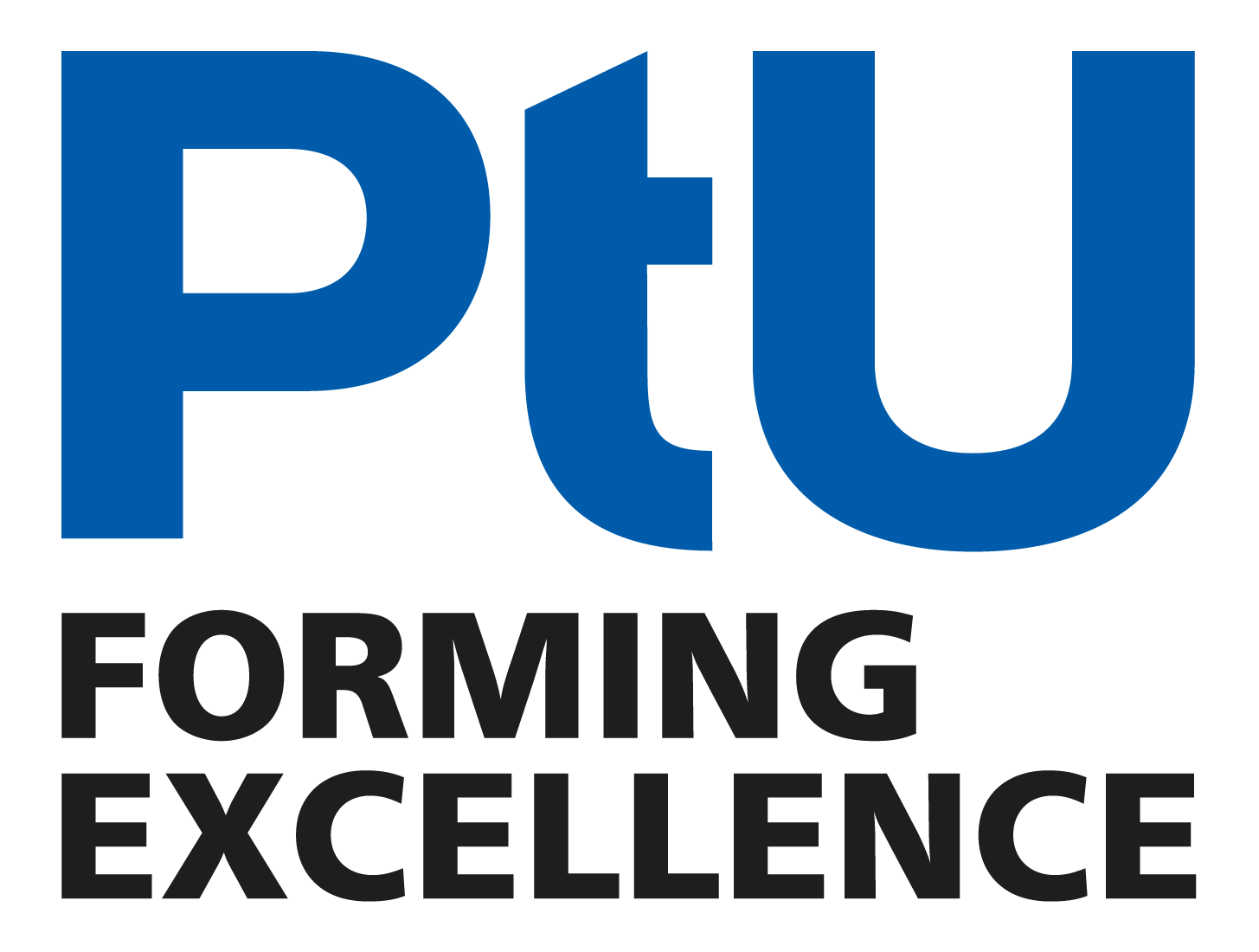