Excursion to the iron foundry Dossmann and Concad GmbH
2020/02/27
Within the scope of the Bachelor lecture “Production Technology”, students were given the opportunity to experience the complete manufacturing process of a sheet metal part: from the CAD model over casting, to toolmaking, and from the forming process itself to the subsequent trimming.
The first stop on the excursion took us to the Dossmann iron foundry in Rippberg. Here we first learned about the long history and tradition of the iron foundry and gained an insight into the current business field of the foundry. The general introduction was followed by a lecture on the correct design of parts to be casted, building on the basis taught during the lectures. In contrast to the classroom, being in an actual foundry gave us the opportunity to see the design principles in actual molds and patterns. We saw the production of the patterns in the company-owned carpentry. After the patterns are made, they are covered with a special sand mixture, which hardens and after removal of the pattern leaves behind the actual mold used for casting.
The highlight of our first stop was without a doubt the tapping of the induction furnace and witnessing the subsequent casting of several tons of liquid metal.!
The second stop of the excursion waited for us after only a short drive to Walldürn., where Concad GmbH, a manufacturer specializing in the production of drawing tools as well as prototype and small batch production of sheet metal components, is located.
After a brief general introduction to the activities of the company, we were divided into two groups and toured the plant. We began our tour in the design department, where we saw the CAD modelling of the drawing tools for automotive body shell components, followed by an insight in the simulation of such drawing processes.
We continued our tour in the milling shop, where pre-cast tools are milled according to the CAD specifications. The sheer size of some of the machines there was astounding: tThe largest of the portal milling machines has a traveling distance of 15x5x2.5 meters – larger than most participants’ homes!
Following the production process further downstream, we reached the press workshop, where the previously milled and assembled tools are used to manufacture automotive body parts. Here we observed how complex 3D geometries are drawn from a flat sheet of metal.
The final stop was the trimming of the sheet metal parts via laser and a final measurement for quality assurance.
After a long, but very informative day, we began our journey back to Darmstadt. The students were delighted to see their theoretical knowledge in practical applications.
We would like to take this opportunity to thank Mr. Ott and Mr. Dell from Dossmann Eisengießerei, as well as Mr. Breunig and Mr. Förtig from Concad GmbH, for taking the time to guide us on an interesting tour through their respective companies and for answering the questions that arose comprehensively and competently.
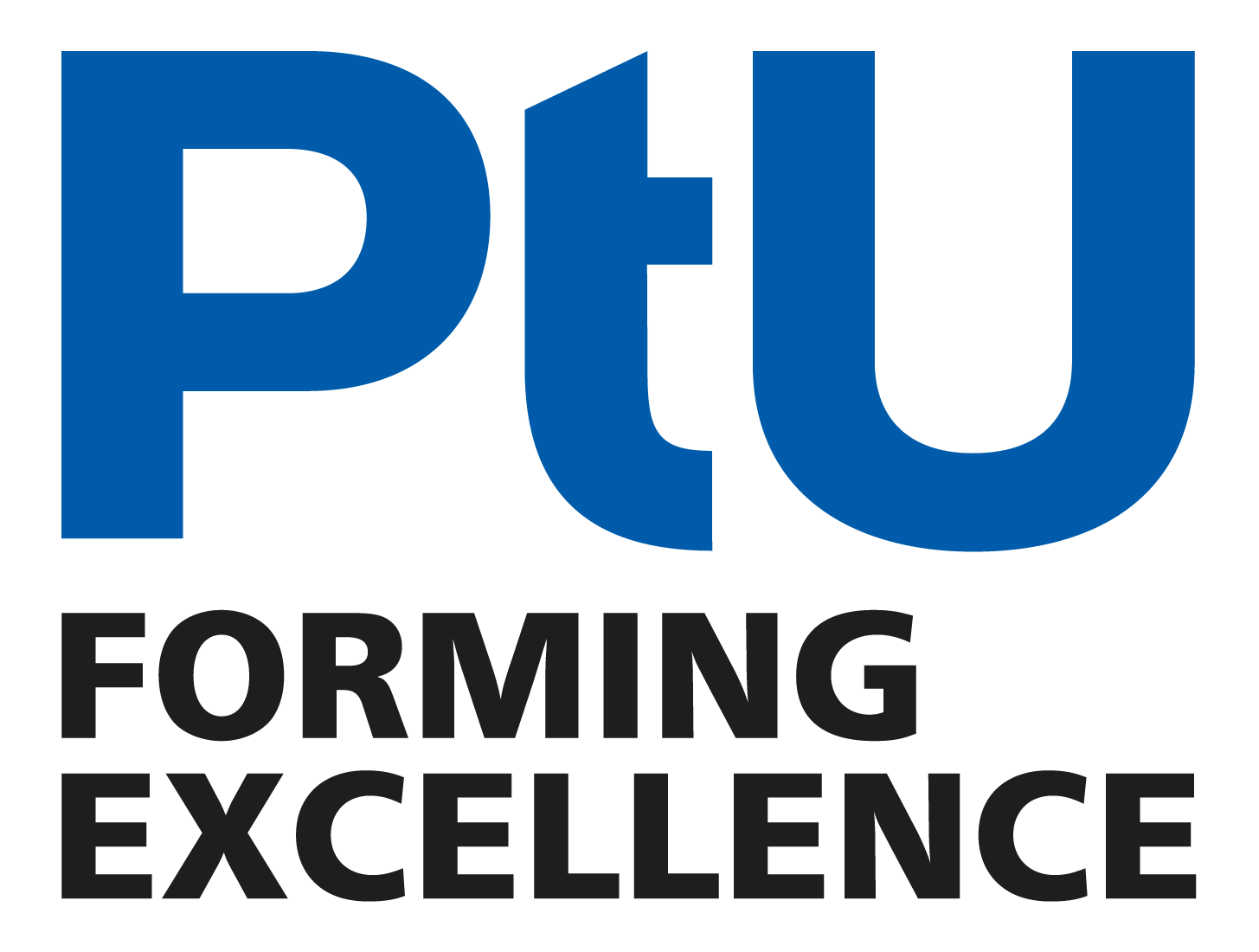