UMFO – Ressourcenschonende Umformprozesstechnologie für die Herstellung von Struktur-Leichtbauteilen im Fahrzeugbau
Im Projekt UMFO wird durch den Kooperationspartner LASSO Ingenieurgesellschaft mbH das neue Verfahren Flexibles Bandbreitenreduktionswalzen (FBRW) zum Walzen breitenveränderlicher Bänder simulativ entwickelt. Die Weiterverarbeitung der so hergestellten Halbzeuge zu breitenveränderlichen Profilen durch flexibles Rollformen soll am PtU erforscht werden. Dazu wird anhand eines hergestellten Prototyps der Einfluss der durch das FBRW eingebrachten Materialinhomogenitäten auf die Profilfehler beim flexiblen Rollformen untersucht.
Mit dieser neuen Prozesskette soll die kontinuierliche Fertigung individualisierter, großdimensionaler und breitenveränderlicher Bänder zur Herstellung von belastungsangepassten Strukurbauteilen mit in Längsrichtung veränderlichen Querschnitten kostenreduziert und ressourcenschonend ermöglicht werden. Eine mögliche Anwendung sind Fahrwerkslängsträger im LKW- und Sattelaufliegerbau.
Motivation
Flexible Profilierverfahren, wie bspw. das flexible Rollformen, ermöglichen, neben der Bauraumoptimierung oder Funktionsintegration, eine hohe Produktindividualisierung unter Beibehaltung eines kontinuierlichen Fertigungsprozesses. Gleichzeitig gelten belastungsangepasste Träger mit in Profillängsrichtung veränderlichen Querschnitten als ein Schlüsselelement des Leichtbaus.
Als Halbzeug ist ein in der Breite variabler Blechzuschnitt erforderlich, wobei durch den Zuschnitt Verschnitt entsteht. Das FBRW zielt darauf ab, durch das direkte Umformen breitenveränderlicher Bänder das Zuschneiden überflüssig zu machen und somit Leichtbau und Ressourceneffizienz zu verbinden. Die neu zu entwickelnde Prozesskette ermöglicht somit eine Flexibilität von Anfang an.
Derzeit wird das flexible Rollformen von breitenveränderlichen Profilen zur Produktion von Fahrwerkslängsträgern im Sattelaufliegerbau eingesetzt. Insgesamt werden weltweit jährlich rund 1.3 Millionen Sattelauflieger (Stand: 2021) für den Güterverkehr hergestellt [*], wodurch sich ein großes Potential zur Materialeinsparung ergibt. Lastangepasste Träger könnten jedoch auch im Bahn-, Schiffs- und Flugzeugbau sowie zur Trägerherstellung im Bauwesen, in der Raumfahrt, für Regalsysteme und Strommasten zum Einsatz kommen.
[*] https://www.statista.com/statistics/743480/truck-trailer-production-worldwide/ (Website abgerufen: 20.11.2022)
Lösungsweg
Der neuartige Lösungsansatz des FBRW für die Herstellung von Struktur-Leichtbauteilen aus Stahl wird in Abbildung [1] schematisch dargestellt. Im ersten Schritt wird an einem Knüppel mittels eines flexiblen Stauchgerüstes ein vorher berechnetes Dickenprofil eingewalzt. Dieses Dickenprofil wird durch eine inverse Modellierung bzw. mithilfe von Simulationen ausgehend vom gewünschten Breitenverlauf ermittelt. Im Anschluss wird es über mehrere Warm- und Kaltwalzenstufen zu einem Band mit der benötigten Endgeometrie gewalzt. Das fertige Band wird im Schritt 2 aufgecoilt und an den verarbeitenden Betrieb geliefert. Im verarbeitenden Betrieb wird das Band im Schritt 3 direkt im flexiblen Rollformverfahren zum fertigen Struktur-Leichtbauträger umgeformt.
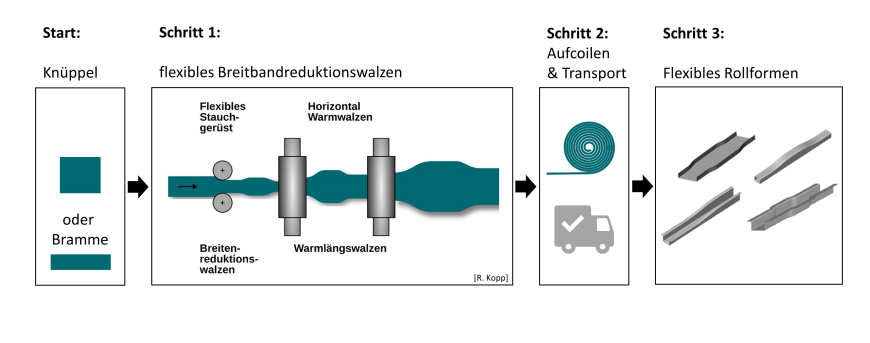
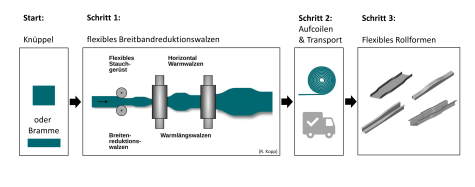
Eine wesentliche Herausforderung wird die Weiterverarbeitung aufgrund der resultierenden inhomogenen Eigenschaften der breitenvariablen Bänder durch unterschiedliche Abwalzgrade sein. Dadurch können beim Rollformen typische Profilfehler wie beispielsweise die Rückfederung, Torsion oder beim flexiblen Rollformen auftretende Beulen im Profilboden an unterschiedlichen Stellen unterschiedlich stark ausfallen.
Am PtU soll die Modellentwicklung für das flexible Rollformen – spezifisch für das FBRW mit Berücksichtigung der Materialinhomogenitäten – sowie das Prozessfenster auf Basis von Simulationen und Experimenten untersucht und entwickelt werden. Anhand der Analyse der Eigenschaften des gefertigten Prototyps im Labor soll zudem eine Modellvalidierung, Modellreliabilität und Generalisierung für die neue Umformtechnologie erfolgen.
Danksagung
Dieses Projekt wird vom Bundesministerium für Wirtschaft und Klimaschutz (BMWK) aufgrund eines Beschlusses des Deutschen Bundestages gefördert.
Zusätzlich geht der Dank an den Projektpartner LASSO Ingenieurgesellschaft mbH für die Kooperation bei der Durchführung des Projekts.
Gefördert durch
Projektpartner