Residual Stresses – Targeted Manipulation of Residual Stresses during Cold Forging
Within the framework of this research project, the residual stresses introduced by cold forming and their effects on the component performance are to be analyzed scientifically. This includes the reproducible production, the measurement, in particular in geometrically complex areas, as well as the development of suitable methods for the prediction and evaluation of residual stresses. By means of a process control, residual stresses are also to be introduced into a component in a targeted manner in order to increase the quality of the components.
Motivation
In cold-formed components, locally different residual stresses develop over the entire component volume. A precise knowledge of the distribution and the amount of the production-induced residual stresses is of particular importance in the design of cyclically loaded components. This relates in particular to materials in which the strength is not adjusted by a heat treatment, but exclusively by the strengthening mechanisms resulting from cold forming.
While a certain level of basic knowledge of residual stress formation is existing in simple cold-forging processes, there is still a considerable need for research in terms of the stress distribution as a function of the individual process steps in multi-stage process manufactured components. Moreover, the effects of different residual stresses on the performance of complex stressed components are not yet fully understood.
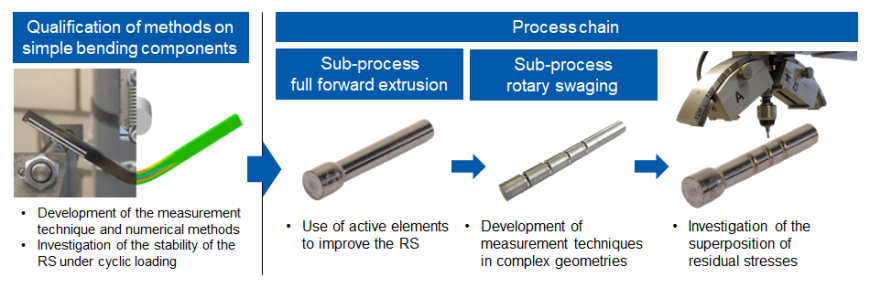
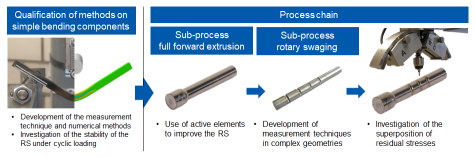
Approach
As an example of improvement of performances through the adjustment of residual stresses, the process chain of austenitic steels is taken into account within the framework of the project. An analysis of the single steps of production is performed. Parallel to the experimental investigation, the optimization of existing numerical models for the residual stress distribution is carried out as a function of different process parameters during cold forming. The aim is to be able to make a quantitative statement regarding the residual stress state with the help of the numerical simulation. Finally, the reproduction of residual stresses, which can be achieved across the entire process chain, is analyzed. From the knowledge and the understanding of the mechanisms, measures are taken to improve the properties of the workpieces.
Acknowledgement
The presented research project is funded by the German Research Foundation (DFG) – GR1818/63-1, GR1818/63-2 and GR1818/63-3 within the priority program SPP2013 – “Targeted utilization of forming induced residual stresses in metallic components”.
Furthermore, we would like to thank the company Strecon A/S for the active support of the project.
Funded by
Project Partner