Echtzeitfähige Verschleißmodelle – Aufbau einer Methode zur Erkennung von Verschleißzuständen in mehrstufigen Blechumformprozessen
Das Ziel des Forschungsprojektes ist die Untersuchung der Verschleißentwicklung in mehrstufigen Umformprozessen und der Implementierung einer automatisierten Verschleißüberwachung. Mit dem Einsatz des neu entwickelten Systems zur Echtzeit-Verschleißdetektion können Anwender sofort auf temporäre Verschleißerscheinungen reagieren und diesen entgegenwirken. Dadurch werden große Mengen Ausschuss vermieden sowie die Kosten für Werkzeugstilland und Reparaturen gesenkt. Neben Anwendern erhalten auch Hersteller von Schmierstoffen datengestützt Erkenntnisse über die Performance ihrer Schmierstoffe im Langzeitversuch. Dies versetzt spezialisierte Unternehmen, in die Lage, ihre Kunden gezielt zu beraten und gegeben falls eine inline Verschleißüberwachung zu implementieren.
Motivation
In der Blechbearbeitung haben Verschleißphänomene einen direkten Einfluss auf die geometrischen und funktionalen Produkteigenschaften und beeinflussen damit direkt die Wirtschaftlichkeit solcher Prozesse. Somit ist die systematische Erforschung von Werkzeugverschleiß und dessen Auswirkung auf den Prozess für Unternehmen aus technologischen und wirtschaftlichen Gründen interessant.
Aus Gründen des Leichtbaus kommt der fortschreitende Einsatz hochfester Werkstoffe (z.B. bestimme Aluminiumlegierungen) sowie die Verarbeitung von Kupfer, Messing, und Nickel im Rahmen der Digitalisierung und Elektrifizierung hinzu. Aluminium kommt vermehrt im Karosseriebau und Kupfer für elektrische Komponenten zum Einsatz. Beide Werkstoffe neigen deutlich stärker zur Adhäsion als Stahlwerkstoffe und können dadurch schneller adhäsiven Verschleiß verursachen. Neben kontinuierlichen Verschleiß können kleine Schwankungen in den Prozessparametern einen großen Einfluss auf die Verschleißbedingungen haben (siehe Abbildung 1). Plötzlichen Auftreten vorübergehender adhäsiver Verschleißerscheinungen können unerwartete die Verschleißrate erhöhen und die Qualität einer Produktcharge beeinträchtigen. Dieser Effekt spielt insbesondere bei mehrstufigen Prozessen in Folgeverbundwerkzeugen eine große Rolle, da durch die enge Verkettung der Einzelprozesse die Folgen von temporärem Verschleiß in einer Werkzeugstufe nicht nur räumlich auf diese beschränkt bleibt. Vielmehr können sich Verschleiß und Qualitätsmängel einer Stufe ebenfalls negativ auf die folgenden Stufen auswirken. Eine durchgehende Analyse des Verschleißzustandes von Bauteil und Werkzeug kann den Anwender direkt über mögliche temporäre Verschleißerscheinungen bzw. Verschleißzustände informieren. Hier soll eine Kombination aus optischer Oberflächenvermessung und sensorischer Analyse einzelner Prozessparameter (z.B. Kraft- und Temperaturverlauf) präzisere Erkenntnisse liefern. So können zeitnah Korrekturmaßnahmen ergriffen werden, um wartungsbedingte Stillstandzeiten und Ausschuss auf ein Minimum zu reduzieren. Weiterhin können durch dieses Vorgehen engere Toleranzen eingehalten und auch die Oberflächenqualität der Bauteile verbessert werden.
Lösungsweg
Die Analyse zeigt, dass bisherige Ansätze zum Umgang mit Verschleiß in der Blechumformung erhebliche Defizite aufweisen. Einerseits werden empirische Formeln zur Grobauslegung herangezogen, andererseits werden im industriellen Umfeld Verschleißerscheinungen am Werkstück und weniger am Werkzeug gemessen. Diese Überwachung erfolgt beispielsweise in Lichtkabinen, in denen die Bauteile unter besonderer Beleuchtung von erfahrenen Mitarbeitern beurteilt werden Während über analytische Ansätze zwar a priori die Werkzeuglebensdauern abgeschätzt werden kann, gelingt die Prognose von temporär begrenzten Verschleißevents sowie die granulare Beschreibung des aktuellen Verschleißphänomen s sowie dessen Lokalisierung am Werkzeug nicht. Das Forschungsprojekt geht davon aus, dass sich mit Hilfe von inline-erfassten Prozessgrößen und bekannten White-Box-Modellen Grey-Box-Modell etablieren lassen, die eine weitaus detaillierte Beschreibung aktueller Verschleißphänomene ermöglichen. Dabei steht die Kombination analytischer Ansätze mit datengetriebenen Modellen, wie Machine und Deep Learning, zur Abbildung eben dieser realen Verschleißzustände im Vordergrund. Das Kernstück des zu verfolgenden Forschungsansatzes bildet eine zentrale Datenbank, die das zentrale Management von sensorische erfassten Prozessgrößen und digitalisierten Oberflächen sowie eine Integration von datengetriebenen Modellen ermöglicht. Durch die Anwendung der Kombination aus analytischen und numerischen Modellen auf reale Umformprozesse sowie deren Rückführung ergibt sich ein iteratives Vorgehen bei Entwicklung der Verschleißmodelle. Insbesondere durch die optische Erfassung der Werkzeuge und deren verschleißbedingten Geometrieänderungen sollen mit Hilfe numerischer Simulation geometrische Werkzeugkenngrößen aufgebaut werden können. Um die Geometrieänderung präzise, schnell und automatisiert zu erfassen, wird vom Fraunhofer IGD ein laser-basiertes Messsystem entwickelt.
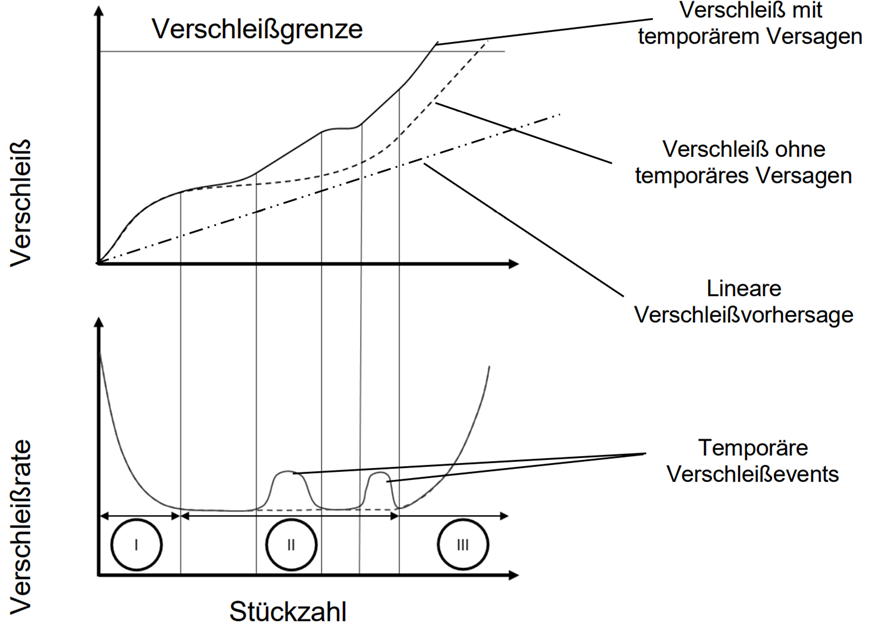
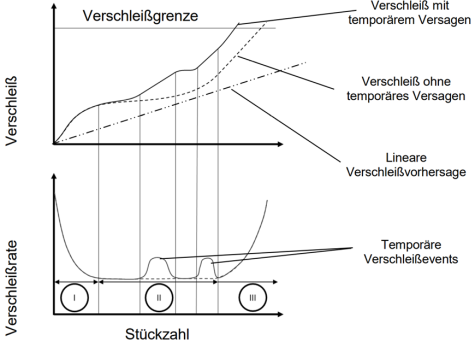
Danksagung
Die hier dargestellten Forschungsarbeiten finden im Rahmen des IGF-Vorhabens Nr. N04434/21 der Forschungsvereinigung Europäische Forschungsgesellschaft für Blechverarbeitung e.V. (EFB) statt.
Dieses wird über die Arbeitsgemeinschaft industrieller Forschungsvereinigungen (AiF) im Rahmen des Programms zur Förderung der industriellen Gemeinschaftsforschung (IGF) vom Bundesministerium für Wirtschaft und Klimaschutz (BMWK) aufgrund eines Beschlusses des Deutschen Bundestages gefördert.
Ferner bedanken wir uns bei allen Industriepartnern, die das Forschungsprojekt „Aufbau einer Methode zur Erkennung von Verschleißzuständen in mehrstufigen Blechumformprozessen anhand In-Situ aufgezeichneter Prozessgrößen “ im Projektbegleitenden Ausschuss unterstützen.
Gefördert durch
Projektpartner