TransForm – Control of paper wrinkling and camera-based data acquisition in transparent tools
The three-dimensional forming of paper by deep-drawing enables the production of sustainable packaging. One of the challenges for extending the range of applications is the wrinkles created during the forming process. An innovative semi-transparent tool will be used to increase the understanding of wrinkle formation. With this knowledge and adaptive process control, the goal is to improve the quality of the formed part through local control of the material flow.
Motivation
Both legal requirements and a growing consumer demand for sustainable packaging require a reduction in the share of plastic-based single-use packaging. One alternative is paper-fibre-based packaging. In order to offer a wide variety of shapes, three-dimensional forming processes such as deep-drawing are required.
The low degree of forming that can be achieved and the defects that occur still pose challenges for a comprehensive substitution of plastic-based packaging with paper as a material. A particularly pronounced defect in deep-drawn paper is the formation of wrinkles in the flange. The underlying mechanism of their occurrence is tangential compressive stresses as a result of material displacement in the forming process, but their exact local and temporal formation and development is not yet sufficiently understood. This circumstance as well as the development of methods to locally influence the forming process will be addressed in the project “TransForm – Control of wrinkle formation of fibre-based materials by adaptive process control and camera-based data acquisition in transparent forming tools”.
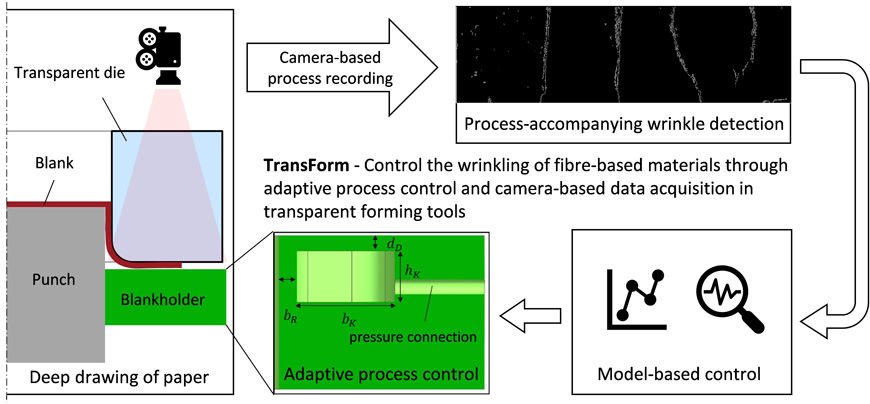
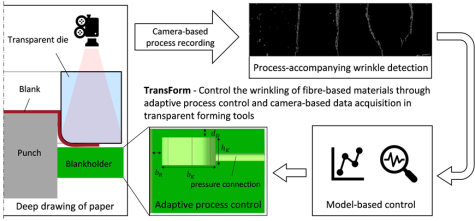
Approach
Key elements are a transparent die and image-based sensor technology for the in-situ detection of material flow and wrinkle formation. Based on the optical process monitoring, insights into the factors influencing the local material flow can be gained with temporal resolution and a comparison with an analytical prediction of wrinkle formation can be carried out.
On this basis, locally adaptive process control will be investigated. Locally adaptive process control is particularly promising for complex forming geometries and due to the strongly anisotropic material properties of the fibre material paper. For this purpose, a locally adaptive blank holder is being developed using additive manufacturing processes. By means of individually controllable elastic pressure pockets, the influence of a locally adapted control and regulation of the hold-down surface pressure on the wrinkle pattern can be investigated (see figure). The aim is to maximize the quality of the molded part in terms of wrinkling.
Acknowledgement
The presented research project is funded by the Deutsche Forschungsgemeinschaft (DFG, German Research Foundation) – GR 1818/85-1.
Funded by