ROTAFLEXEXPERT – Entwicklung einer Methode zur Prozessauslegung und -überwachung beim Rundkneten
Im Projekt ROTAFLEXEXPERT wird die echtzeitliche Erfassung von Prozessgrößen beim Rundkneten nahe der Umformzone erforscht. Ein im Projekt entwickeltes Messystem ermöglicht die Verfahrensoptimierung hinsichtlich wirtschaftlicher, technischer und ressourcenschonender Ziele. Die gewonnen Erkenntnisse eröffnen überdies einen Technologiesprung hin zur individualisierten Umformung rotationssymetrischer Bauteile.
Motivation
Das Rundkneten ist ein Verfahren der Kaltumformung zur Bearbeitung rotationssymmetrischer Bauteile. Dabei wird der Durchmesser von Stäben oder Rohren reduziert, indem rotierend angetriebene Werkzeuge mit hoher Geschwindigkeit umlaufend radial auf das Bauteil einwirken und so eine inkrementelle Umformung erzielen. Das Rundkneten setzt einen hohen Entwicklungs- und Werkzeugaufwand voraus und ist daher derzeit meist nur für die Fertigung von Bauteilen im Rahmen von Großserien mit sehr hohen Stückzahlen und langer Produktlebenszyklen, beispielsweise für die Automobilindustrie, wirtschaftlich.
Derzeit werden die Werkzeuge und die Prozessparameter mittels zeit- und kostenintensiver Trial-And-Error-Versuche entwickelt, erprobt und eingestellt. Oftmals wird der Prozess aufgrund fehlender Prozesskenngrößen rein über das von dem/der Bediener:in subjektiv aufgenommene Maschinenverhalten und die resultierenden Prozessgeräusche bewertet und dann über die verschiedenen Prozessparameter(-fenster) in Erprobungsrunden auf Basis von Erfahrungswissen eingestellt und optimiert.
Die hohe Abhängigkeit von personengebundenen Erfahrungswerten zum Einstellen und Betreiben von Prozess und Maschine setzt einen hohen Spezialisierungsgrad voraus. Dadurch entstehen hohe Kosten und das Verfahren ist nur für große Serien wirtschaftlich einsetzbar. An diesem Punkt, soll das Projekt ROTAFLEXEXPERT ein umfassendes Prozessverständnis durch Sensorik schaffen, sodass das Rundkneten zukünftig datengetrieben ausgelegt werden kann. Das führt zu neuen Einsatzmöglichkeiten des Prozesses in der Industrie.
Lösungsweg
Der Lösungsansatz beruht auf der Erfassung des Drehvorschubwinkels. Dieser gilt als resultierende Größe und kann bisher weder gezielt eingestellt werden, noch bestehen geeignete industrietaugliche Ansätze, diesen zu messen. Der Drehvorschubwinkel wird über Messpunkte vor und nach der Umformzone sowie der Antriebsdrehvorgabe erfasst. Somit ist auch eine Ermittlung der qualitätskritischen Bauteiltorsion und dem Bauteildurchrutschen in der Spannzange möglich.
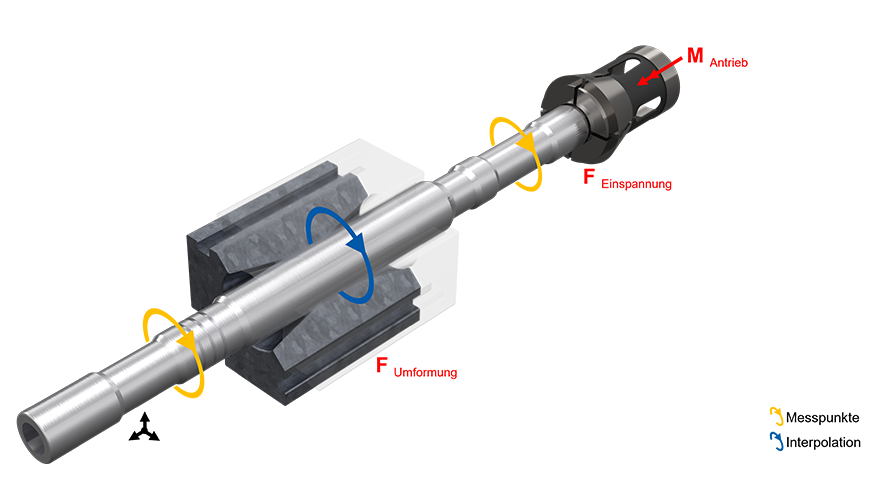
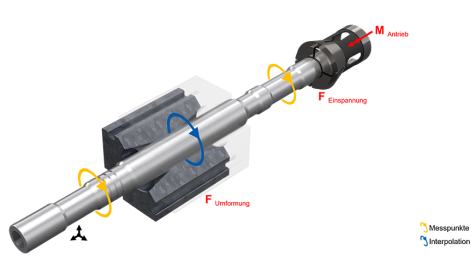
In einem ersten Schritt wird ein hochsensitives Messsystem zur Erfassung des Drehvorschubwinkels durch Simulationen und Praxisversuche implementiert. Aus diesem System wird erstmals ein datengetriebenes Einfahren des Prozesses für ein neues Bauteil realisiert. Durch die Erkenntnisse aus der hochsensiblen Lösung kann eine robuste Lösung adaptiert werden, die für den Einsatz in der Produktion geeignet ist. Die für die Forschung relevante feine Auflösung wird reduziert und durch ein belastbareres System ersetzt. Dieses soll gewährleisten, dass die relevanten Prozessgrößen auch bei Produktionsbedingungen in dauerhaft rauem Umfeld in ausreichender Genauigkeit erfasst werden können.


Sind die vorrangegangenen Schritte erfolgt, wird ein Modell zur Bestimmung optimaler Prozessbedingungen für das Rundkneten auf Basis der sensoriell erfassten Messgrößen aufgestellt. Dieses Modell wird für den industriellen Einsatz adaptiert und erprobt.
Danksagung
Dieses Projekt wird vom Bundesministerium für Wirtschaft und Klimaschutz (BMWK) aufgrund eines Beschlusses des Deutschen Bundestages gefördert.
Zusätzlich geht der Dank an den Projektpartner IPG – IFUTEC Produktions GmbH für die Kooperation bei der Durchführung des Projekts.
Gefördert durch
Projektpartner