IFEtargetryHUB – Inertial Fusion Energy (IFE) Targetry HUB für die DT-Trägheitsfusion
Das Projekt IFEtargetryHUB untersucht die Fertigung und Metrologie von für die lasergetriebene Trägheitsfusion essenzielle sogenannte Targets. Das Institut für Produktionstechnik und Umformmaschinen (PtU) übernimmt dabei die numerische Simulation und Optimierung einer Prozesskette für die Mikro-Umformung. Dazu wird eine detaillierte Materialcharakterisierung der verwendeten Werkstoffe durchgeführt, einschließlich der Ermittlung der Grenzformänderungskurven und des Schädigungsverhaltens während des Umformprozesses. Diese Daten dienen der Erstellung und Validierung eines präzisen Material- und Prozessmodells.
Darüber hinaus entwickelt das PtU die Planung, Fertigung und Inbetriebnahme von Umformprozessen mit Wirkmedium sowie mit starren Werkzeugen. In diesem Zusammenhang werden die Prozessparameter optimiert und beide Fertigungsmethoden miteinander verglichen.
Motivation
Die lasergetriebene Trägheitsfusion ist ein gepulster Prozess, bei dem mehrere hochenergetische Laser ein sogenanntes Target, das die Wasserstoffisotope Deuterium und Tritium enthält, komprimieren und erhitzen. Bei extremen Temperaturen von bis zu 120 Millionen Grad Celsius verdampft das Target und der Brennstoff wird unter enormem Druck komprimiert. Dadurch können die Atomkerne ihre elektromagnetische Abstoßung überwinden und fusionieren. Diese Reaktion setzt eine enorme Energiemenge frei und hat das Potenzial, eine saubere und nachhaltige Energiequelle zu sein.
Bisher existiert keine Technologie, die diese Targets in einer kommerziell nutzbaren Form für Fusionsreaktoren herstellen kann. In diesem Projekt werden das Wissen und das Fachwissen aller beteiligten Partner des Verbundprojektes gebündelt, um gemeinsam Materialien und Herstellungsprozesse zu entwickeln, die eine effiziente und skalierbare Produktion sowie die Charakterisierung von Targets für die lasergetriebene Trägheitsfusion ermöglichen. Diese Targets stellen einen Engpass für die Effizienz der Kernfusion dar und sind daher eine Schlüsseltechnologie auf dem Weg zu zukünftigen lasergetriebenen Fusionsreaktoren.
Lösungsweg
Ein mechanischer Umform- und Trennprozess mit Stanzmaschinen stellt eine wirtschaftliche, zeit- und ressourceneffiziente Möglichkeit der Teilefertigung dar, erfordert jedoch aufgrund geringer Größen und hoher Genauigkeitsanforderungen der Kugelkalotte und des Konus (siehe Abbildung 1) eine präzise Auslegung und Optimierung der Umformprozesskette. Durch die Expertise in der Blechverarbeitung beteiligt sich das Institut für Umformtechnik (PtU) an dem Gesamtvorhaben durch die Untersuchung der umformtechnischen Herstellbarkeit der Komponenten. Für die präzise Abbildung des Werkstoffverhaltens und des Umformprozesses werden zunächst numerische Finite-Elemente-Simulationen durchgeführt.
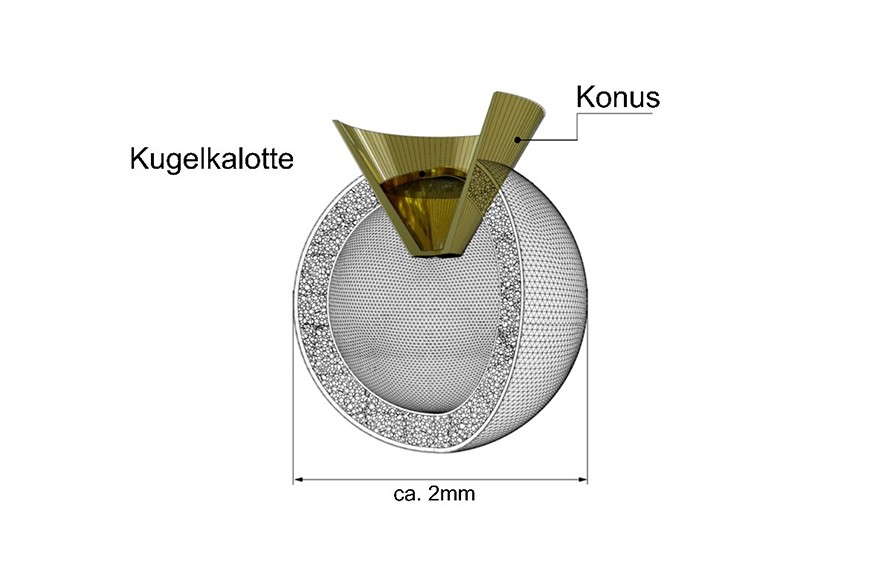
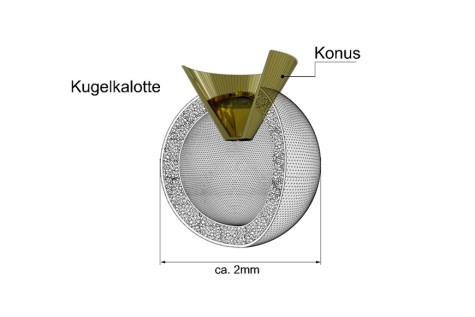
Zunächst wird die Charakterisierung von Aluminiumfolien unter einachsiger und biaxialer Belastung durchgeführt, wodurch grundlegende Parameter für die Modellierung gewonnen werden können. Durch die zusätzliche Bestimmung von Grenzformänderungskurven kann die Fähigkeit des Werkstoffs, Verformungen ohne Versagen standzuhalten, präzise bewertet werden. Ein weiterer wichtiger Aspekt ist die Analyse des Schädigungsverhaltens, begleitet von einer detaillierten Oberflächencharakterisierung sowie der Messung von Reibungskoeffizienten, die für die Genauigkeit des Modells entscheidend sind. Die gesammelten Informationen werden zur Entwicklung und Validierung des Werkstoffmodells verwendet, um sicherzustellen, dass das simulierte Verhalten die experimentelle Realität genau wiedergibt. Die Simulation des Umformprozesses wird durchgeführt, um die Machbarkeit und Optimierung der Prozessroute zu bewerten.
Für die Herstellung von Kugelkalotte und Konus werden aufgrund der anspruchsvollen Anforderungen zwei Prozessrouten aus der Umformtechnik betrachtet: die Umformung mit starrem Werkzeug und die Umformung mit Wirkmedium. Die Prozessparameter werden optimiert, um die Produktqualität und die Fertigungseffizienz zu verbessern. Für beide zu fertigende Komponenten werden die Umformverfahren verglichen, um die optimale Strategie hinsichtlich Umformgüte zu bewerten und so eine wirtschaftliche und präzise Targetfertigung zu ermöglichen.
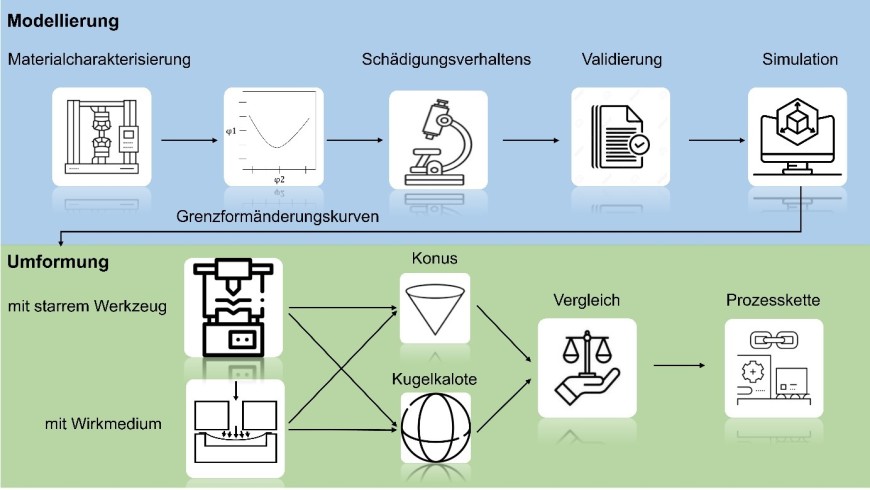
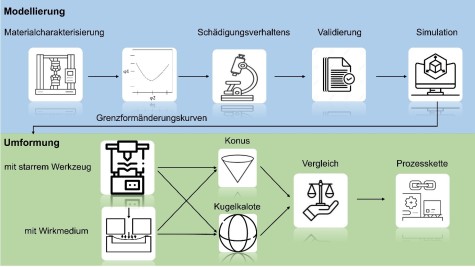
Danksagung
Dieses Forschungs- und Entwicklungsprojekt wird mit Mitteln des Bundesministeriums für Bildung und Forschung (BMBF) im Rahmen der Förderrichtlinie „Basistechnologien für die Fusion – auf dem Weg zu einem Fusionskraftwerk“ mit dem Förderkennzeichen 13F1013I gefördert und vom Fraunhofer- Institut für Angewandte Festkörperphysik (IAF) koordiniert. Das PtU bedankt sich bei allen industriellen und akademischen Partnern, die am Forschungsprojekt IFEtargetryHUB beteiligt sind.
Gefördert durch
Projektpartner