Paraffin Phase Change Actuators – Design methods for novel, energy-efficient, closed expansion actuators with high force effect
The second project phase serves the further qualification of the PCA for the purpose of functional enhancement and optimization. One objective is the development of a model-based approach for the generation of tailored actuator characteristics. The addressed parameter field comprises the actuating force, the stroke and the active temperature range. For this purpose, geometrical adjustments of the housing, structures integrated into the housing and paraffin additives or mixtures are investigated. Further objectives of the second project phase are the implementation of an integrated activation concept, the thermal decoupling of different zones in the actuator and a transfer of the concept to other actuator geometries, such as a circular ring shape.
Motivation
Within the framework of the completed first project phase of the four-year overall project, the functional verification of the actuator concept was fully achieved. Extensive numerical investigations allowed design guidelines to be derived and an optimal actuator design to be defined. Furthermore, the influences of various modifications were identified. In the next step, a production chain was created which combines efficient forming technology methods with the powerful laser processing centre for cutting and joining. In addition, a process window for the demanding laser welding process has been derived at the laser machining center. The characterization of the resulting demonstrators fully demonstrates the functionality of the actuators (Figure [2]). In the final step, the applicability of the PCA for the motivated cases could be shown by means of active and passive demonstrators.
For the successful application of PCA in practice, however, a number of other aspects remain to be addressed. These include the fact that the actuator dynamics are currently very low. Actuating times of 20 minutes until the specified force is reached are not suitable for practical usage. Furthermore, application-oriented activation concepts have to be developed. Currently, the characteristic curve of the actuator can be influenced only slightly. Further approaches must be determined to enable a wide adaptation of the characteristic curve to different fields of application. With regard to energy efficiency, a double-acting wedge gear is also to be developed, which follows an actuating movement in both the positive and the negative direction. Due to its self-locking character, the actuating effect can thus be maintained without further energy supply. The implementation in practical demonstrators concludes the project and offers the optimal starting point for a transfer into application.


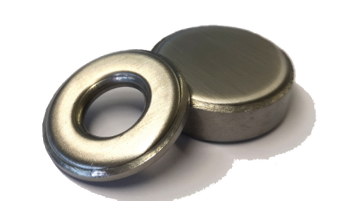
Approach
A project plan with four central aspects has been formulated for the implementation of the above-mentioned points. The first aspect is the enlargement of the characteristic diagram. For this purpose, various approaches to influencing the actuator characteristics are investigated. First, radial deformations in the actuator housing are analyzed. These lead both to a significant increase in radial stiffness and to a reduction in the internal volume of the PCA, so that air inclusions from manufacturing processes can be compensated and the process reliability increased. By investigating paraffin wax mixtures, the operating range of the actuators can be adjusted over a wide temperature band; paraffin wax with melting points below room temperature are also conceivable here. Various approaches are being investigated to increase the actuator dynamics. These include heat-conducting structures within the PCA, such as copper foams, and paraffin additives. The use of alternative housing materials (EN AW-7075) also enables dynamic improvements without performance losses.
Integrating the heat source into the PCA is also a big step forward in terms of dynamics. Here, the housing is no longer in the path of the heat flow. Furthermore, this targeted activation in conjunction with isolation of individual actuator zones is the basis of the double-acting wedge gear. By selectively activating the core or outer zone of the PCA, the directional actuating movement can thus be applied. For the insulation, wedge gears made of ceramic materials are being investigated, among others.
The third main aspect is the investigation of alternative housing designs. The background here is, on the one hand, to test the transferability of the existing numerical representation and model conception. On the other hand, further applications can be developed in this way. At least one circular ring-shaped geometry and one rectangular actuator geometry are investigated.
The final implementation as a demonstrator is to be carried out in two different cases. For this purpose, both the case of a passive PCA and an active PCA are to be represented in a suitable application. Furthermore, two different actuator geometries are planned in these cases. An example is a circular ring-shaped PCA, which, thanks to its paraffin mixture, maintains the preload of a bolted joint over an extended temperature band. Ambient heat serves as its energy source here.
Acknowledgement
The presented research project is funded by the Deutsche Forschungsgemeinschaft (DFG, German Research Foundation) – project number GR 1818/65-4.
Funded by