Entwicklung einer modellbasierten Fehlerdiagnose für Servopressen
Development of a model-based fault diagnosis for servo presses
Research Associate, Masterthesis, Bachelorthesis
Current monitoring systems for presses are usually based on individual force sensors in the ram or press frame and are generally only used to protect against overload using limit values or envelope curves. Comprehensive detection and in-depth diagnosis of various faults, such as wear in bearings, is therefore not possible. Due to the lack of sensor redundancy, these monitoring systems are still prone to errors in the event of failures or incorrect signals and can lead to an unintentional standstill of the press. However, servo presses offer the possibility of calling up different drive data in the machine control system and using this for a model-based monitoring system.
The scope of this work is to analyse and compare the possibilities of model-based fault diagnosis using fuzzy logic and neural networks. For this purpose, an existing model of the drive train of the 3D servo press is used and analysed by making specific changes to the model parameters. The aim is to characterise various faults (such as the wear of machine elements) with the help of both methods and to be able to use them for condition-based maintenance.
Also approved for aerospace engineering.
Research method
Theoretical, experimental
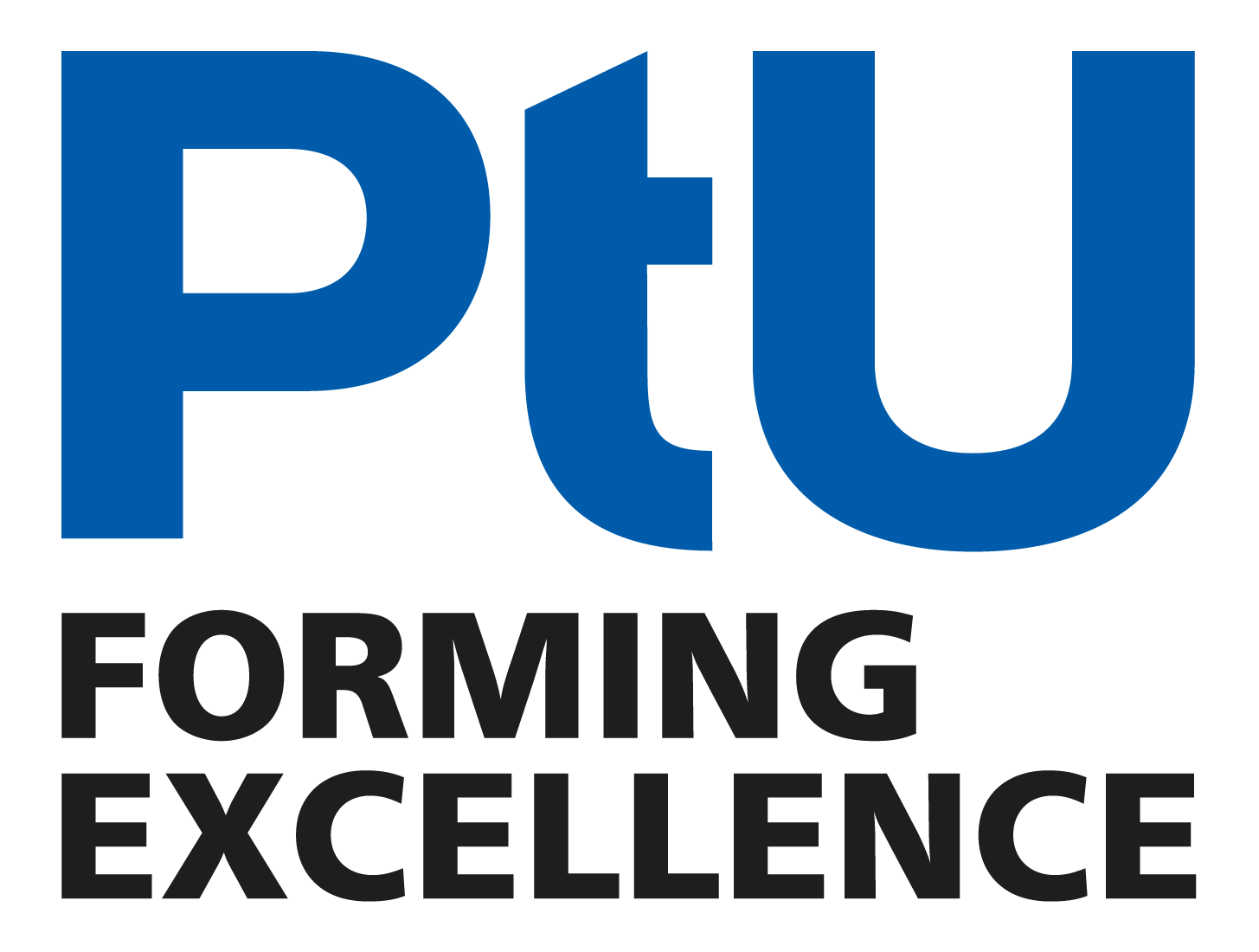