Aufbau eines modellbasierten Zustandsbeobachters für eine Servospindelpresse zur Fehlerdetektion und Diagnose
Development of a model-based condition monitor for a servo screw press for fault detection and diagnosis
Masterthesis, Research Assistant
Current monitoring systems for presses are usually based on individual force sensors in the ram or press frame and are generally only used to protect against overload using limit values or envelope curves. Comprehensive detection and in-depth diagnosis of various faults, such as wear in bearings, is therefore not possible. Due to the lack of sensor redundancy, these monitoring systems are still vulnerable to errors in the event of failures or incorrect signals and can cause the press to stop unintentionally. However, servo presses offer the possibility of calling up different drive data in the machine control system and using this for a model-based monitoring system. As part of this work, an analytical model of the drive train of a servo screw press is to be set up in MATLAB Simulink as the basis for a condition monitor and validated with real data from the press control system. By changing the model parameters in a targeted manner, it will also be investigated how different faults (wear of machine elements) can be characterized in the drive data for fault diagnosis.

Also approved for aerospace engineering.
Research method
Experimental, theoretical
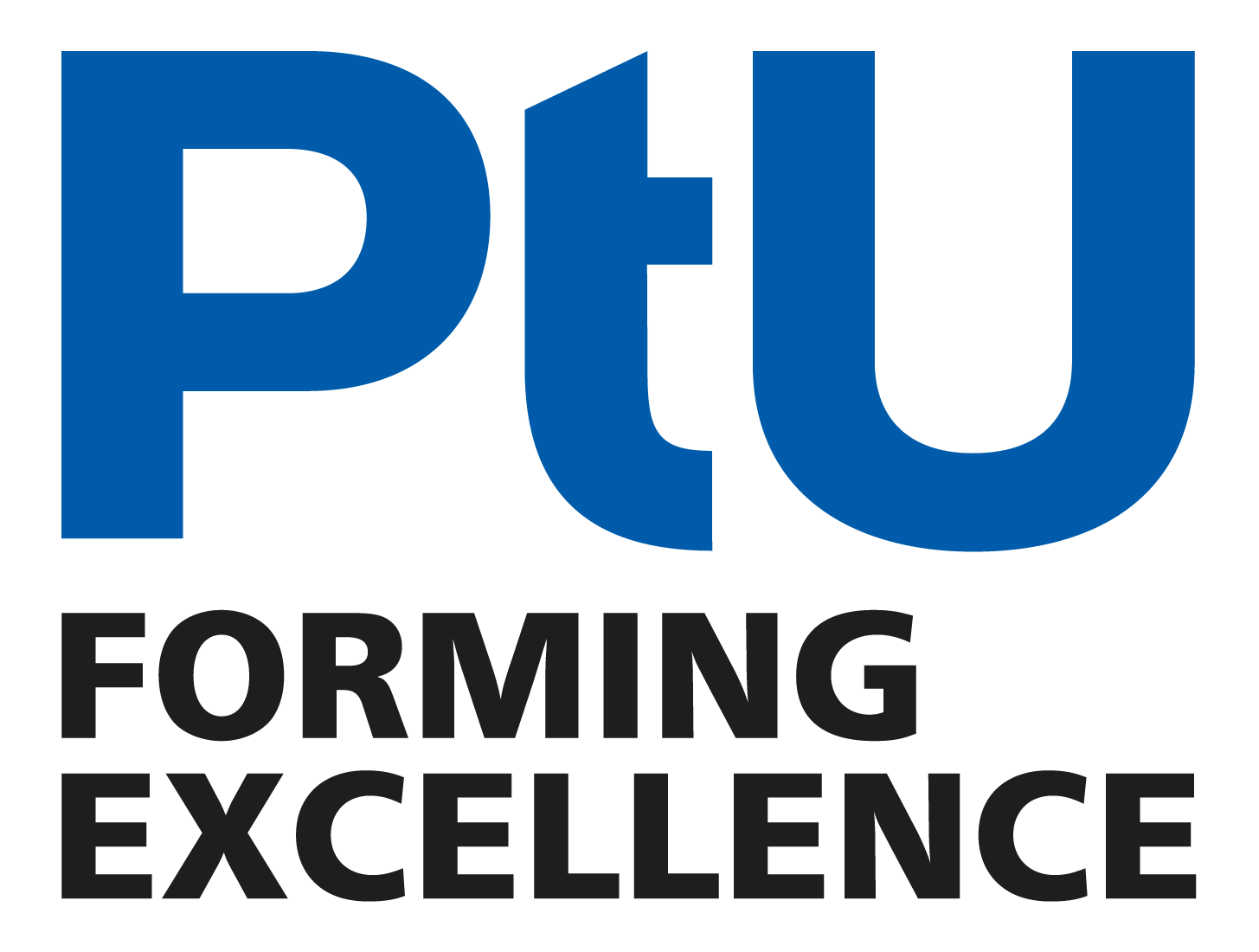