The future of safety: optimized crash structures for electromobility
2025/01/07
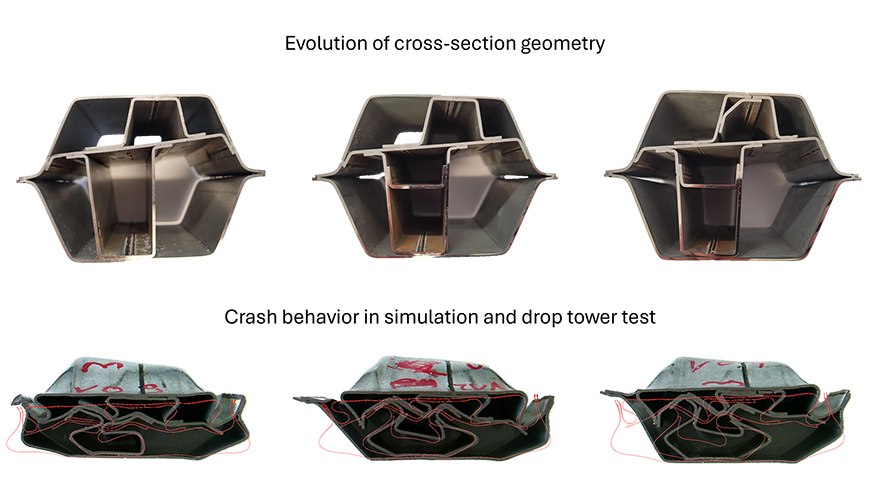
Crash structures are a key part of modern vehicle design – they protect occupants and other road users and are becoming increasingly important in the context of electromobility. With heavier vehicles and sensitive battery packs, the demands on their performance are increasing.
Innovative optimisation methods such as graph and heuristic-based topology optimization (GHT) already offer solutions: They enable precise FE-based optimization of the profile cross-section, often for extruded aluminium profiles. However, the existing process has its limitations – particularly in terms of material selection and weight.
Roll forming as a game changer
The application of GHT to roll-formed profiles for the production of crash structures made of high-strength steel was investigated in cooperation with the Chair of Optimisation of Mechanical Structures (OMS) at the University of Wuppertal. This opened new possibilities:
- High-strength and ultra-high-strength steels enable lighter and stronger structures.
- These materials are also recyclable and weldable – perfect for sustainable mobility.
The results are impressive: by adapting the GHT in combination with roll forming, the material properties are optimally utilised. The validation in drop tower tests shows a good agreement between the simulated and real crash behaviour.
Conclusion: The combination of roll-formed, high-strength steel profiles and optimized design sets new standards in crash safety – especially for electromobility.
We would like to thank FOSTA, the AiF and all project partners for their support in carrying out the research project.
(opens in new tab) StaProCrash – Development and manufacture of crash-optimized multi-chamber steel structures by roll forming.pdf
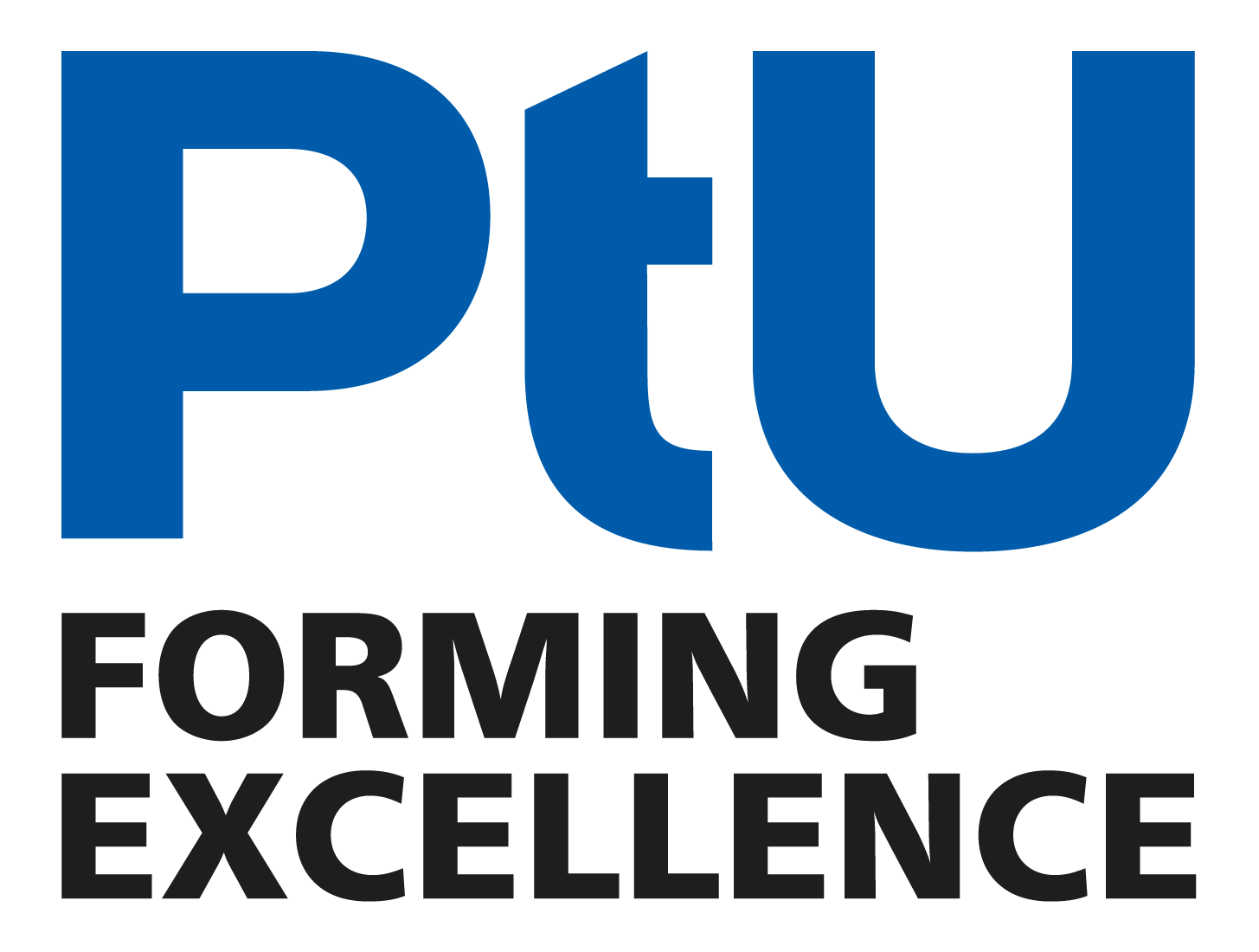