Intelligente Profilieranlage am PtU eingetroffen
04.06.2020
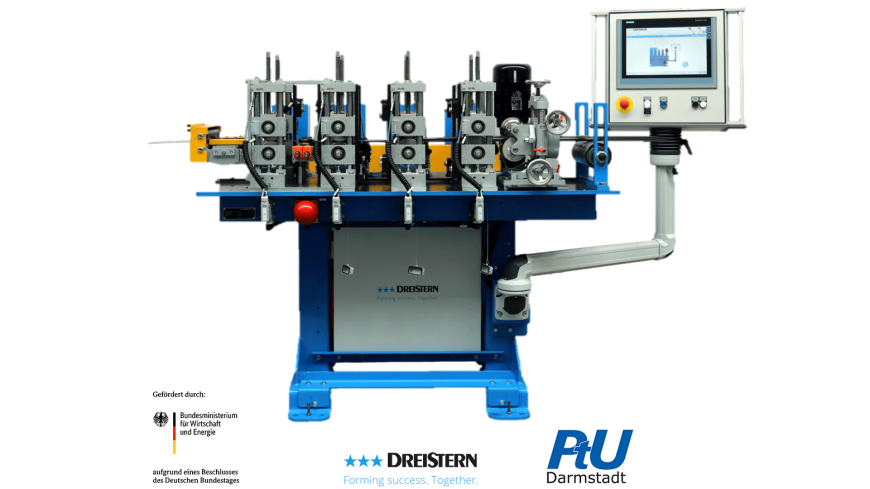
Im Rahmen des durch die AiF-ZIM geförderten Projektes „Intelligente Profilierprozesse durch Überwachung von Antriebsmomenten“ ist zum Ende des ersten Projektjahres eine „intelligente“ Profilieranlage der Firma DREISTERN GmbH & Co. KG aus Schopfheim an der TU Darmstadt eingetroffen.
Das Walzprofilieren ist ein industriell etabliertes Herstellungsverfahren zur kontinuierlichen Umformung offener und geschlossener Profile. Charakteristisch sind die paarweise rotierenden Rollenwerkzeuge, welche in aufeinanderfolgenden Profiliergerüsten sowohl für den Profiltransport als auch für die inkrementelle Umformung zuständig sind. Die dadurch vorhandenen Wechselwirkungen innerhalb der Profilierlinie sind oftmals Ursachen für langwierige Werkzeugjustierungen und geringe Prozesswirkungsgrade. Mit der intelligenten Projektanlage sollen relevante Prozessdaten erfasst werden, um gezielte Maßnahmen zur Prozessoptimierung entwickeln und einleiten zu können.
Nach gemeinsamer Qualifizierung von geeigneten sensorischen Komponenten wurde bei der Dreistern GmbH Co. KG in Schopfheim die Profilieranlage und in Darmstadt das numerische Simulationsmodell des zu untersuchenden Prozesses aufgebaut, um als ausgegebenes Projektziel die Energieeffizienz beim Walzprofilieren sowohl in der Vorauslegung am Computer als auch im realen Prozess untersuchen und steigern zu können. Zum Einsatz im Forschungsumfeld wurde die mobile Profilieranlage mit einem individuellen Unterbau ausgestattet, wohingegen der mechanische und elektrische Teil der Profiliermaschine ausnahmslos aus industriellen Anlagenkomponenten besteht. Der digitale Teil, der die Profilieranlage intelligent und damit für vielfältige Anwendungen der Industrie 4.0 zugänglich macht, baut auf drei charakteristischen Prozessgrößen auf. Zur Kraft- und Positionsmessung an den oberen Werkzeugwellen hat Dreistern eine smarte Integration in die Profiliergerüste entwickelt und diese direkt in die Anlagensteuerung implementiert. Die Drehmomentmessung erfolgt drahtlos über sensorisch ausgestattete Kardangelenkwellen im Antriebsstrang, welche von der core sensing GmbH entwickelt und seitens Dreistern ebenfalls in die Steuerung integriert wurden. Die gemeinsame Erfassung dieser drei Messgrößen ermöglicht es, Prozessveränderungen inline zu erfassen und in der Datenanalyse Korrelationen zwischen den Messdaten und den Prozesszuständen zu identifizieren.
Für das zweite Projektjahr ist vorgesehen, mit der neuen Anlage eine umfassende Datenbasis zu generieren und sowohl in der virtuellen als auch realen Prozessumgebung geeignete Maßnahmen zur Steigerung der Energieeffizienz beim Walzprofilieren zu untersuchen.
An dieser Stelle möchte sich das PtU beim Bundesministerium für Wirtschaft und Energie (BMWI) für die Förderung bedanken. Weiterhin gilt ein besonderer Dank dem Projektpartner Dreistern GmbH & Co. KG für die bisherige Zusammenarbeit sowie die Bereitstellung der Profilieranlage.
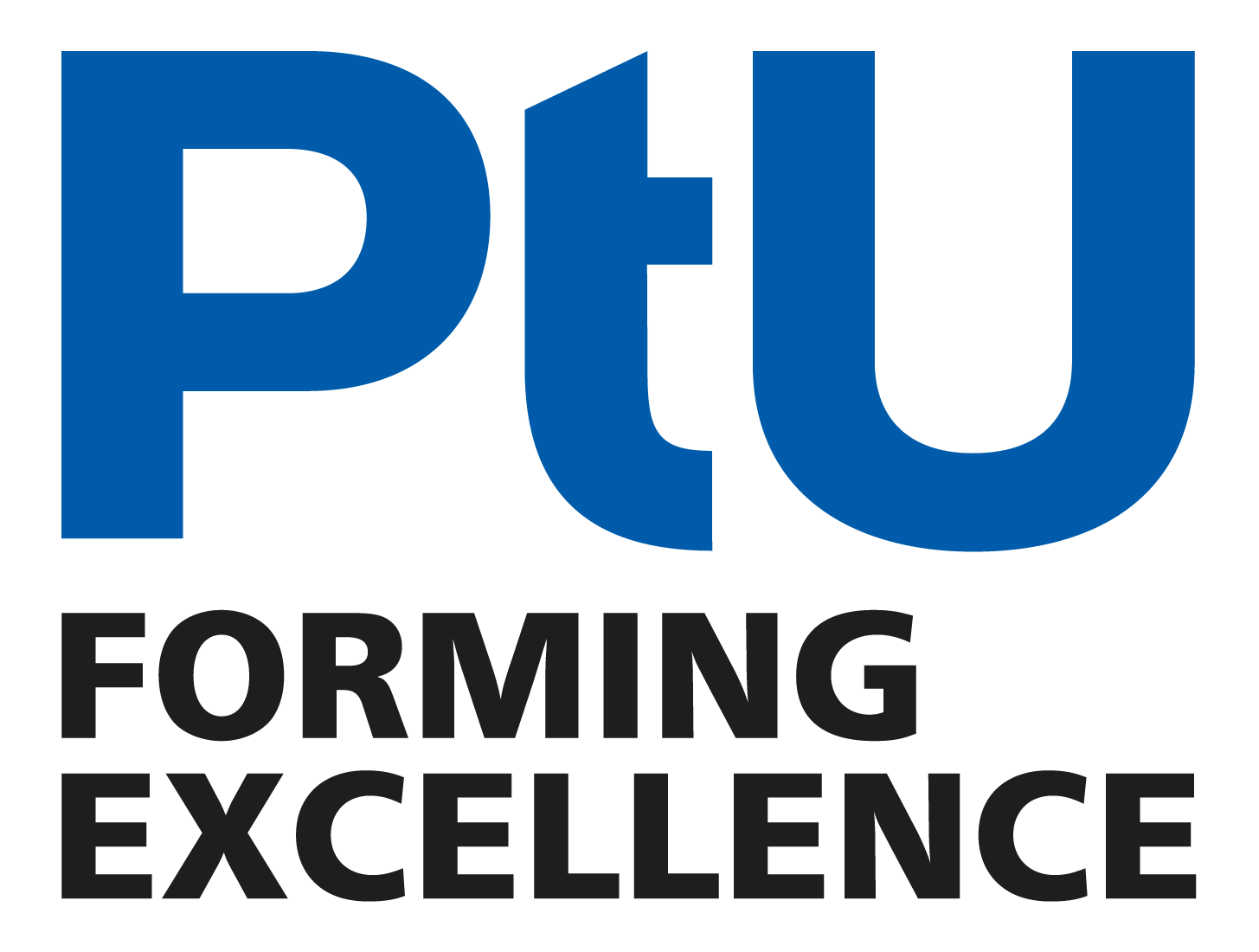