Rosi – Optimization and efficient process design of flexible roller beading
The DFG research project “Optimierung und effiziente Prozessauslegung des flexiblen Rollsickens” deals with the creation of application-oriented fundamentals to achieve industrial acceptance of flexible roller beading. The process of flexible roller beading was developed and implemented within the DFG project GR 18181/53-1. With the help of this process, continuous production of profiles with individually designable, application-oriented height profile cross-sections is made possible. The extension of design freedom in profile construction enables the substitution of existing components, for example in the car body, by height-variable profiles.
Motivation
Ever shorter product life cycles demand increased manufacturing flexibility due to increasing product diversity. Coupled with increasing ecological awareness and the associated political climate targets, this motivates the use of individual components with geometries designed for specific applications. The shift from conventional mass production to mass customization represents an important feature of the current trend in the industrial manufacturing landscape. This shift, together with Industry 4.0 approaches, demand new and further development of manufacturing technologies.
In addition to the production of different product variants on one system without tool changes, flexible processes also enable the manufacture of load-oriented components with efficient material utilization. In forming technology, or more precisely in profile production, load-adapted component design can be achieved by varying material thicknesses, cross-sectional shapes and cross-sectional profiles. This constructive lightweight design has been advanced on the research side, resulting in various roll forming technologies for the realization of flexible sheet metal profiles, all of which, however, have limitations in terms of geometric flexibility or cost-effectiveness.
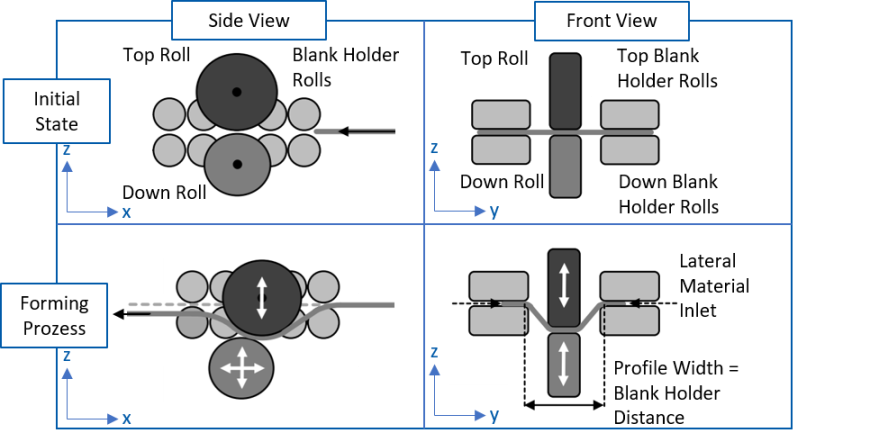
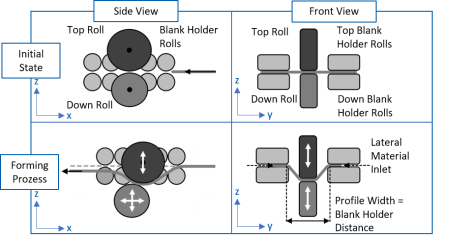
Approach
In order to achieve the goal of industrial acceptance of flexible roller beading, the process is being optimized with regard to tool design and process control. This includes the development of an optimized blank holder concept as well as the optimization of process control to improve profile quality. In addition, practicable methods for efficient process and component design based on analytical models will be developed and validated. The focus here is on the development of an analytical substitute model for predicting possible wrinkling as well as the development of a method for evaluating and reducing sheet thinning during the process.
Acknowledgement
The presented research project is funded by the Deutsche Forschungsgemeinschaft (DFG, German Research Foundation) – project number 501199248. We would like to thank the DFG for their support in carrying out the project.
Funded by